-
oa Global Release Liner Industry Conference 2008
OPTIMISED TECHNOLOGIES ARE EMERGING WHICH REDUCE PLATINUM USAGE IN SILICONE CURING
- Source: Platinum Metals Review, Volume 52, Issue 4, Oct 2008, p. 243 - 246
-
- 01 Jan 2008
Preview this article:
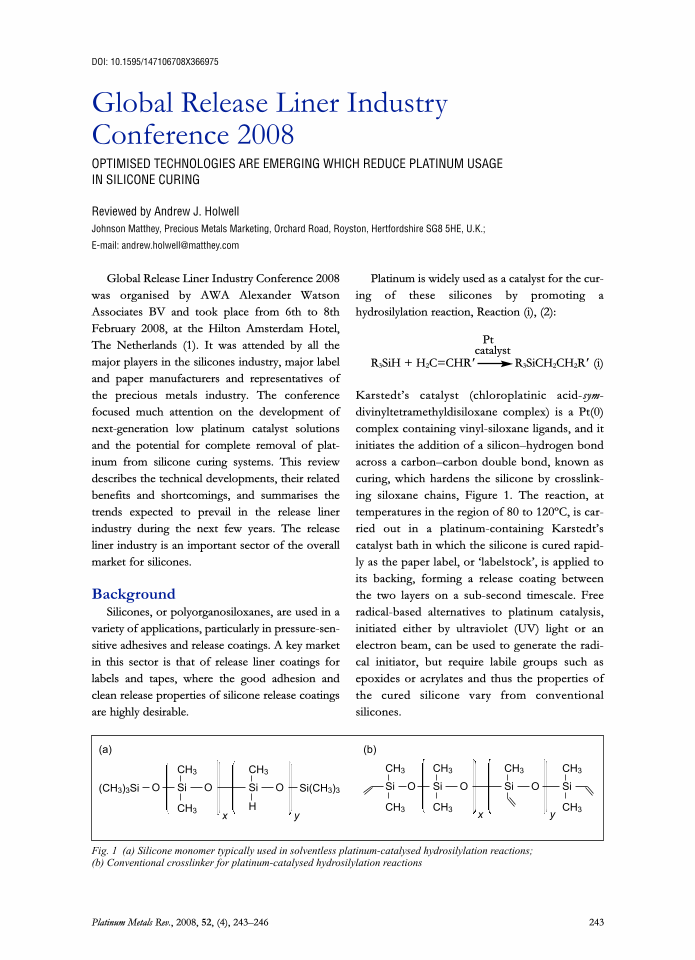



Global Release Liner Industry Conference 2008, Page 1 of 1
< Previous page Next page > /docserver/preview/fulltext/pmr/52/4/PMR-52-4-Holwell-1.gif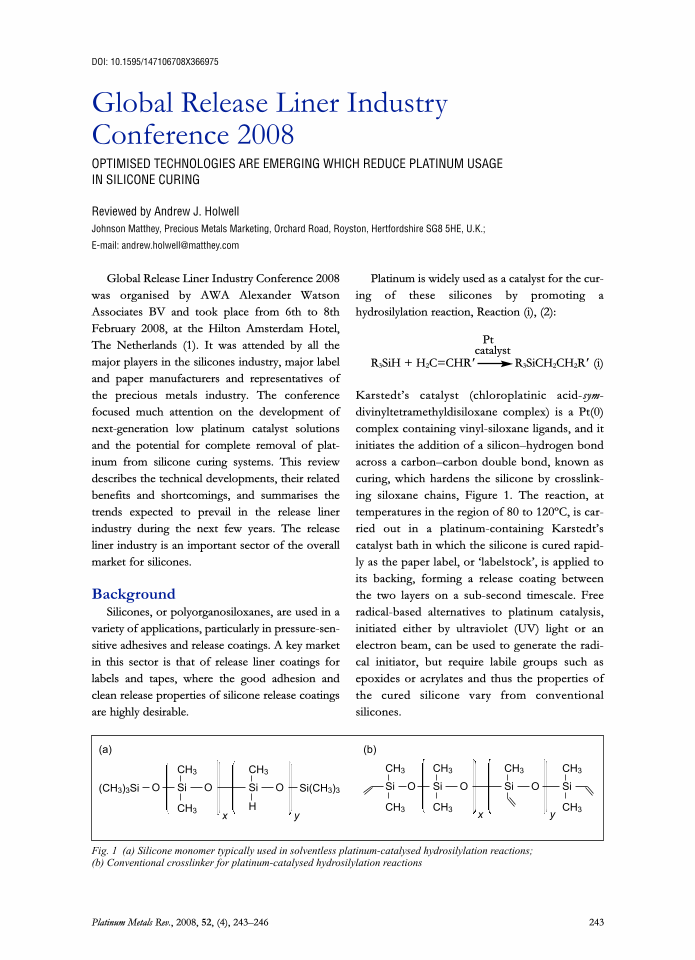
There is no abstract available.
© Johnson Matthey