-
oa Fuel Cells Science and Technology 2008
- Source: Platinum Metals Review, Volume 53, Issue 3, Jul 2009, p. 147 - 154
Preview this article:
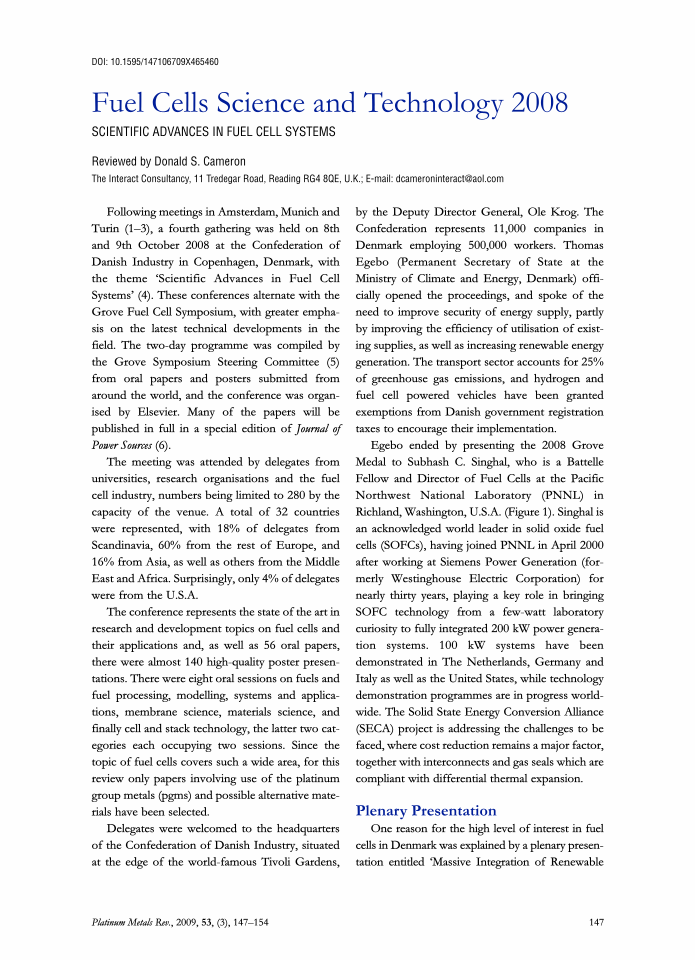



Fuel Cells Science and Technology 2008, Page 1 of 1
< Previous page Next page > /docserver/preview/fulltext/pmr/53/3/s5-1.gif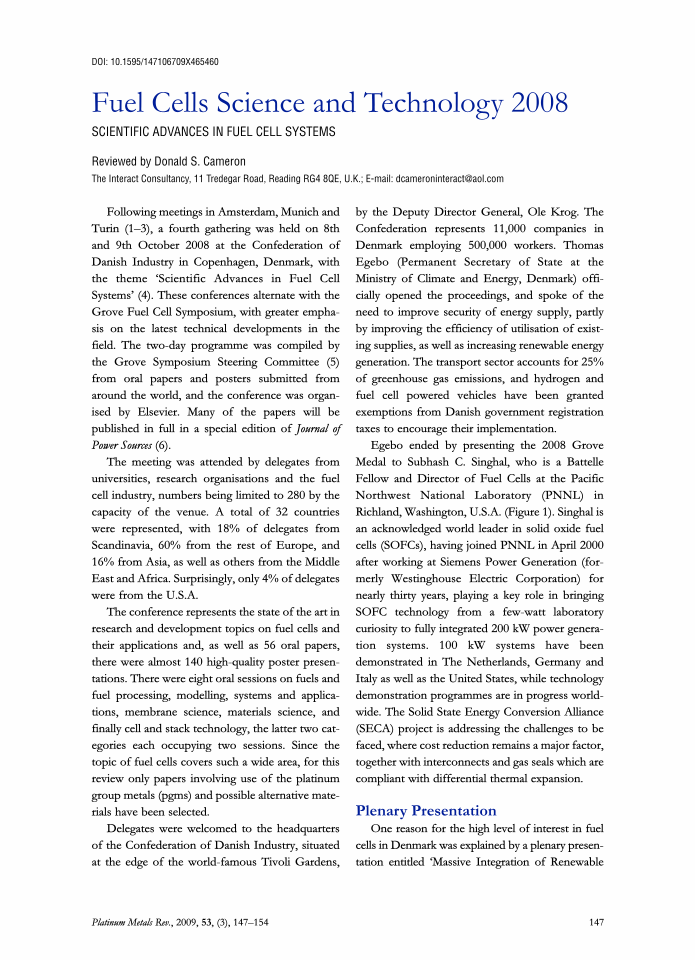
There is no abstract available.
© Johnson Matthey