-
oa FINAL ANALYSIS
The Use of Metal Scavengers for Recovery of Precious, Base and Heavy Metals from Waste Streams
- Source: Platinum Metals Review, Volume 54, Issue 3, Jul 2010, p. 200 - 202
-
- 01 Jul 2010
Preview this article:
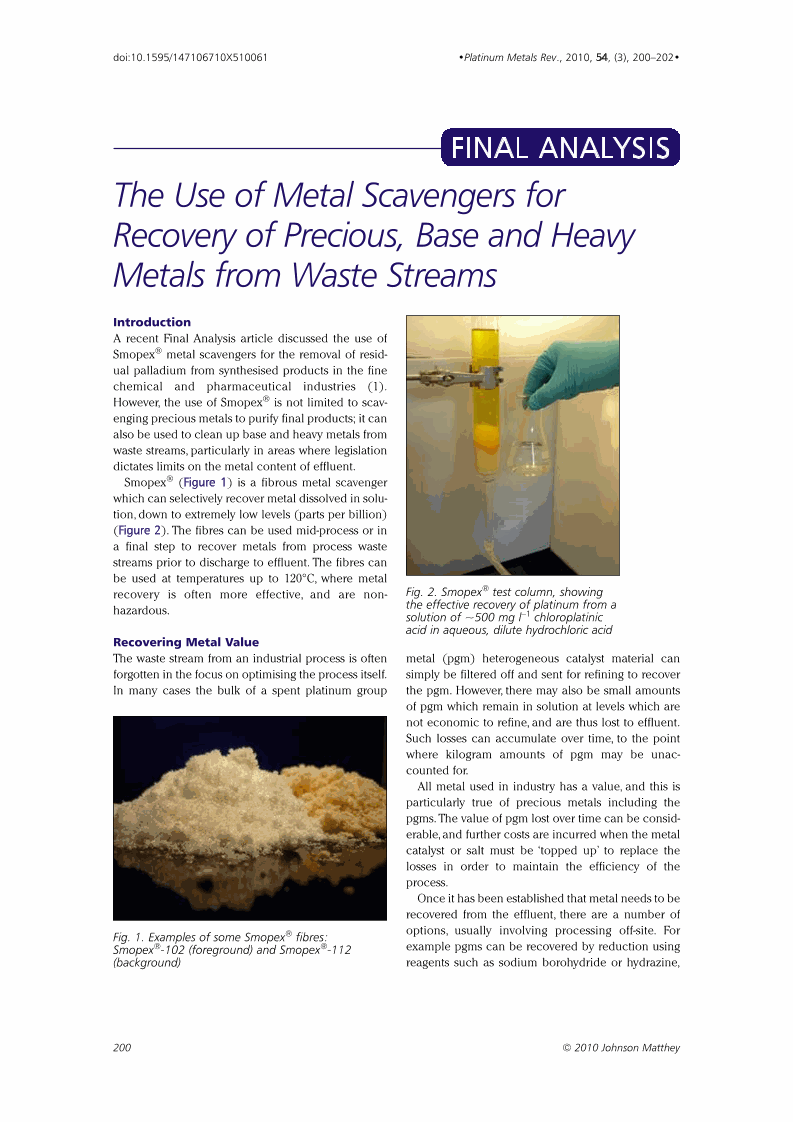



FINAL ANALYSIS, Page 1 of 1
< Previous page Next page > /docserver/preview/fulltext/pmr/54/3/PMR-54-3-Jul-10-Frankham-1.gif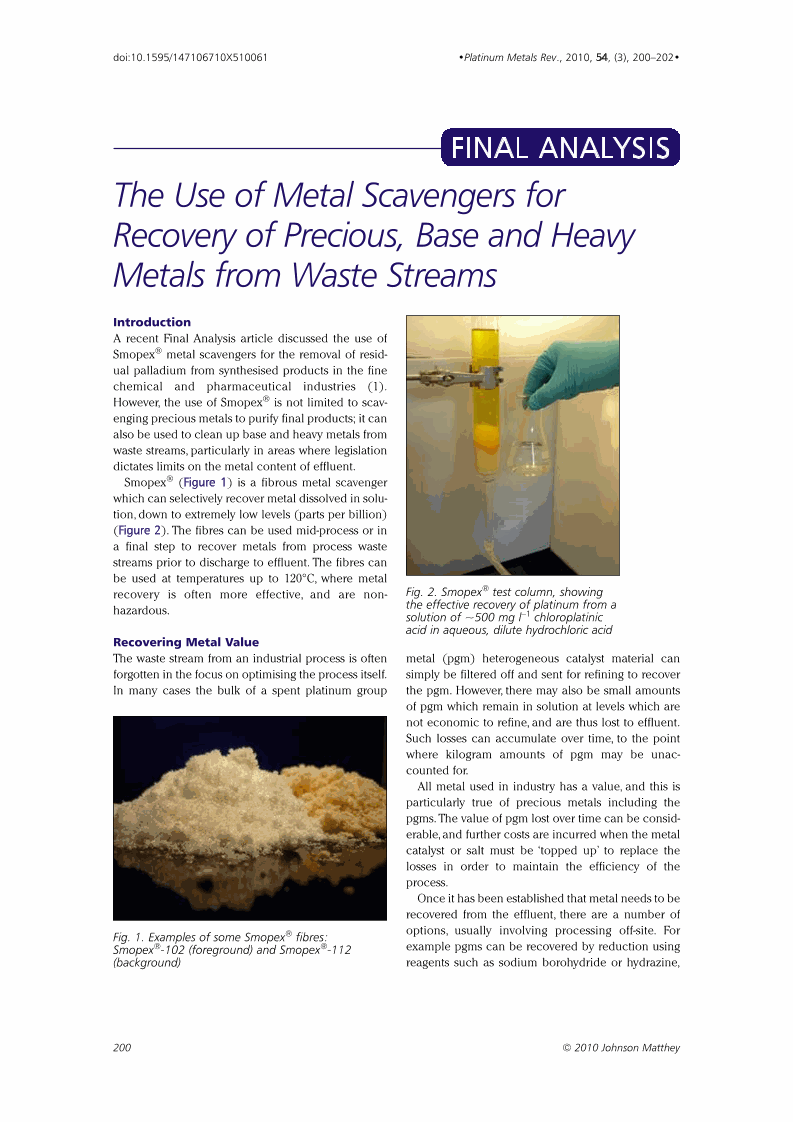
There is no abstract available.
© Johnson Matthey