-
oa The 25th Santa Fe Symposium on Jewelry Manufacturing Technology
Further research on platinum casting by the industry reinforces previous findings
- Source: Platinum Metals Review, Volume 55, Issue 4, Oct 2011, p. 246 - 250
-
- 01 Jan 2011
Preview this article:
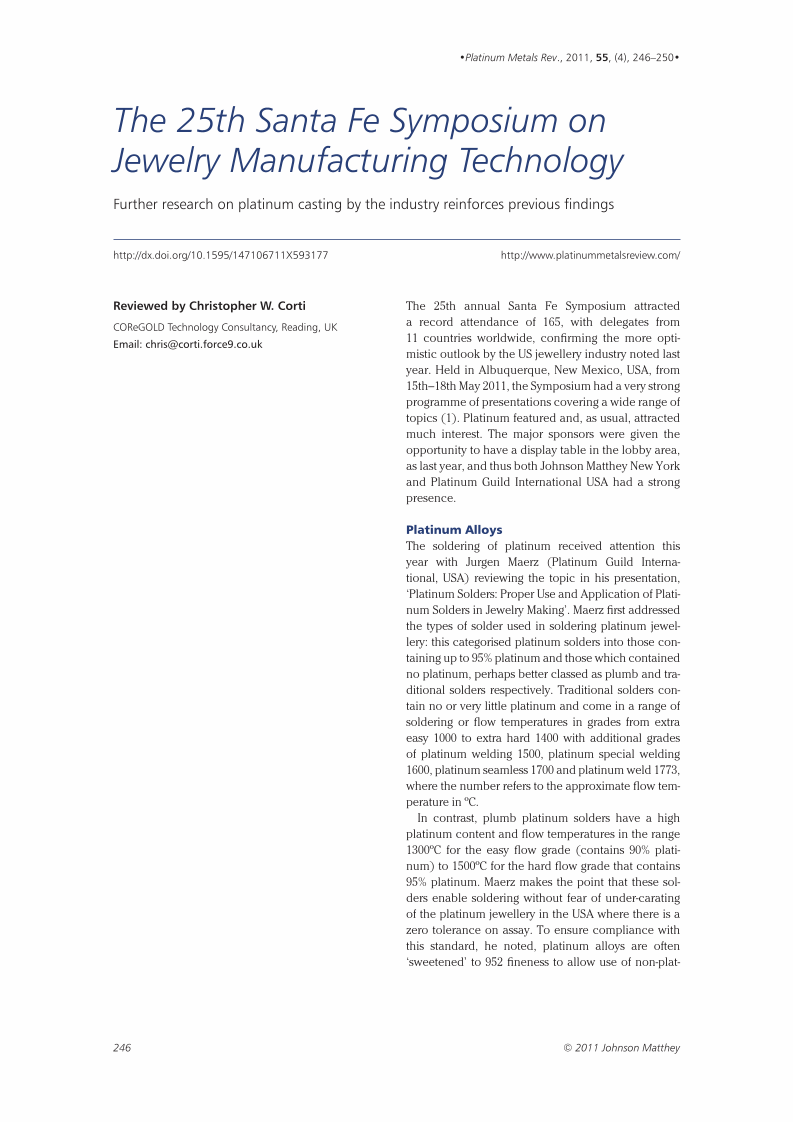



The 25th Santa Fe Symposium on Jewelry Manufacturing Technology, Page 1 of 1
< Previous page Next page > /docserver/preview/fulltext/pmr/55/4/PMR-55-4-Corti-1.gif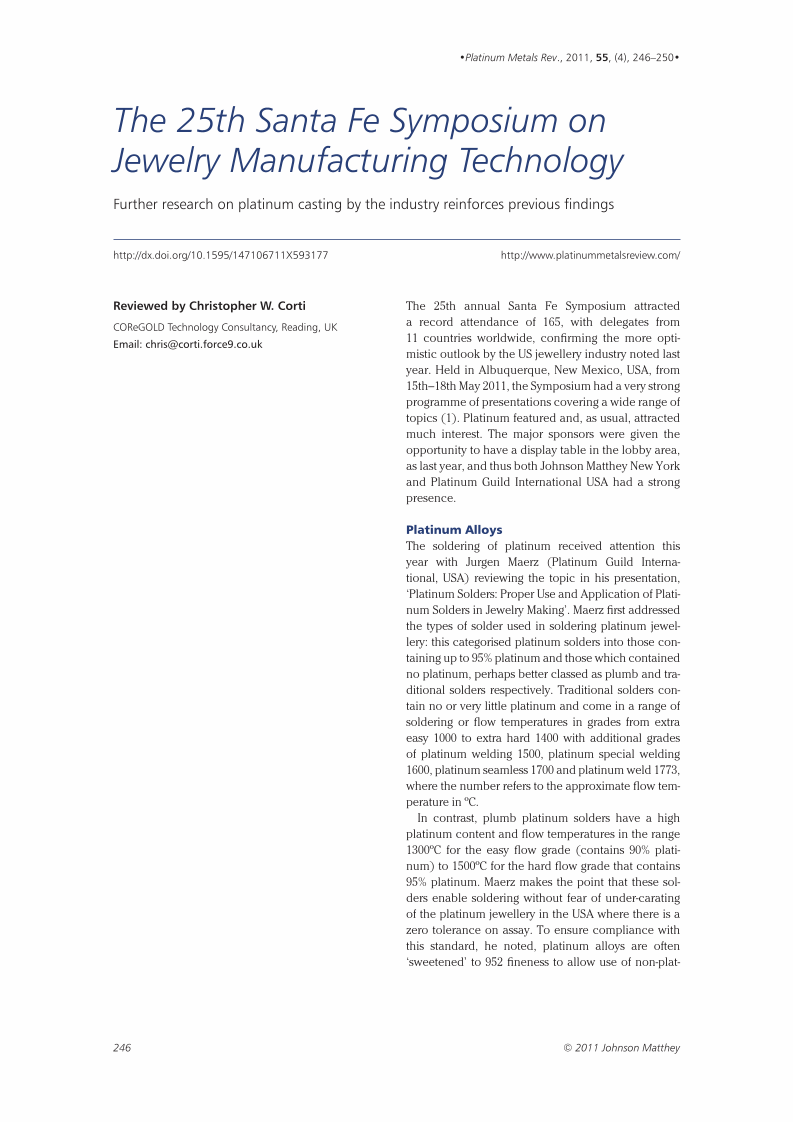
There is no abstract available.
© Johnson Matthey