-
oa Challenges in Catalysis for Pharmaceuticals and Fine Chemicals III
Platinum group metals in practical homogeneous catalysis
- Source: Platinum Metals Review, Volume 56, Issue 2, Apr 2012, p. 99 - 103
-
- 01 Jan 2012
Preview this article:
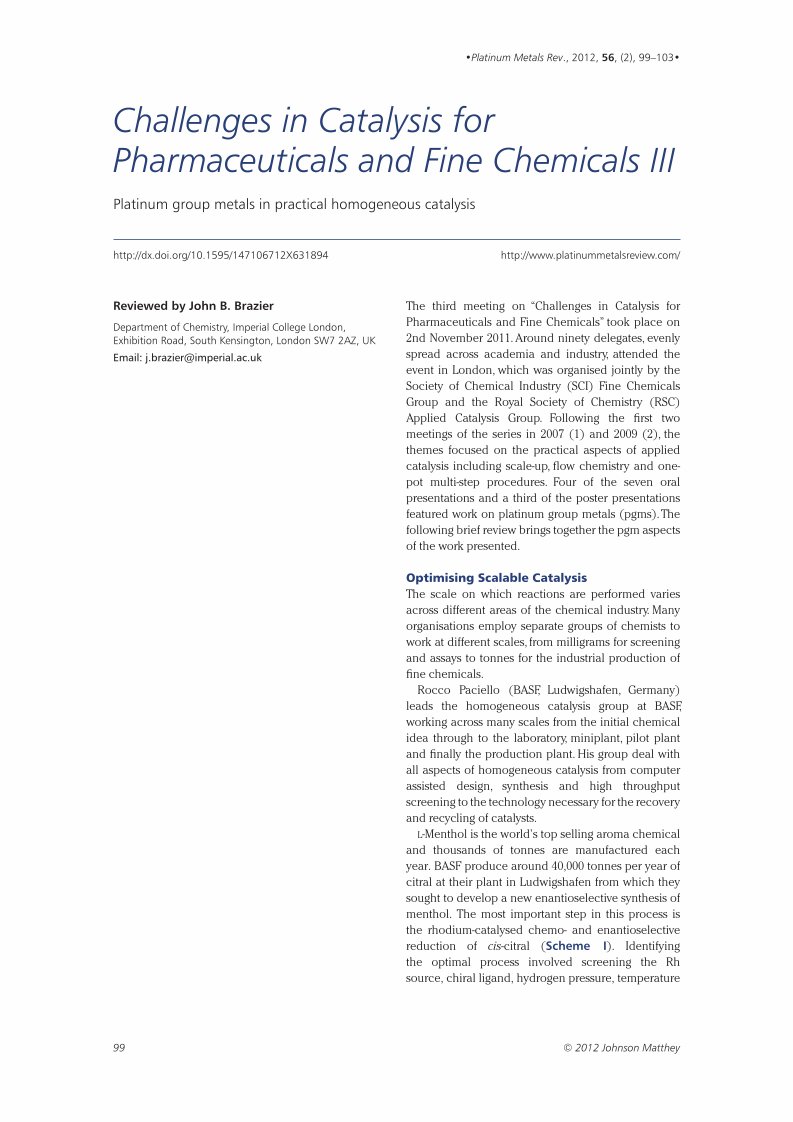



Challenges in Catalysis for Pharmaceuticals and Fine Chemicals III, Page 1 of 1
< Previous page Next page > /docserver/preview/fulltext/pmr/56/2/PMR-56-2-Brazier-1.gif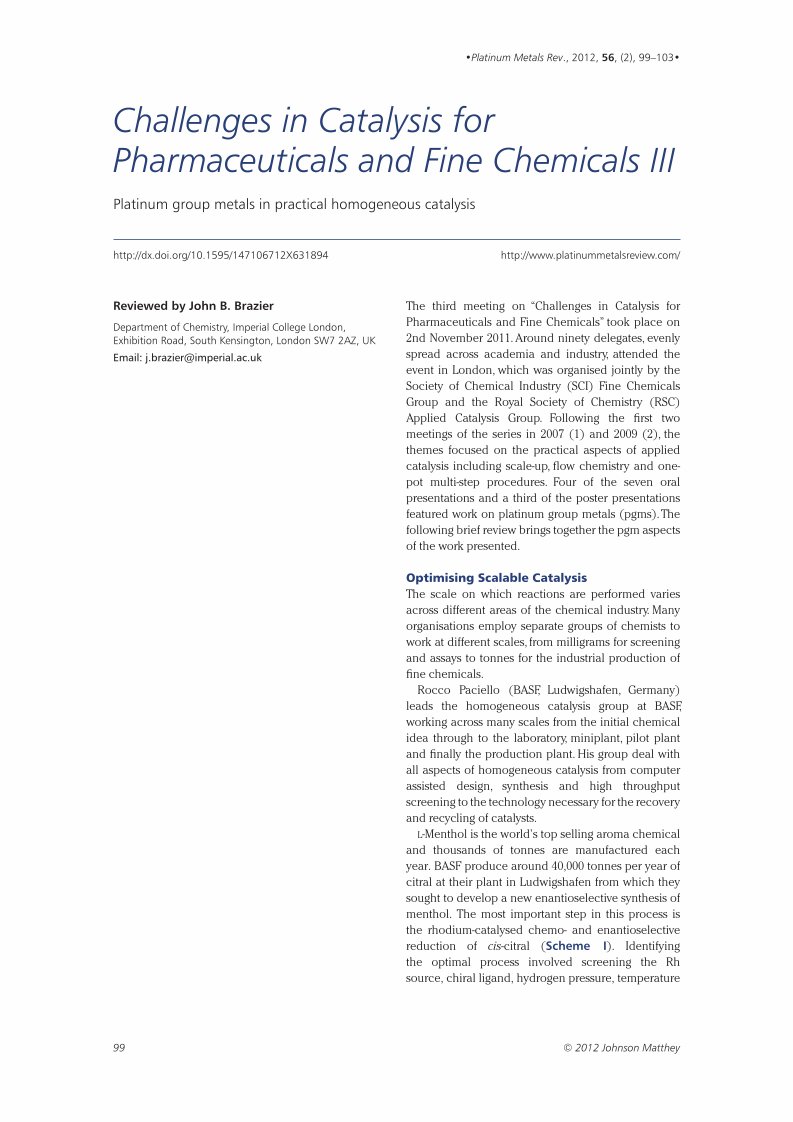
There is no abstract available.
© Johnson Matthey