-
oa FINAL ANALYSIS: Challenges and Opportunities in Palladium: The Claret Jug Experience at the Santa Fe Symposium
- Source: Platinum Metals Review, Volume 56, Issue 4, Oct 2012, p. 284 - 286
-
- 01 Jan 2012
Preview this article:
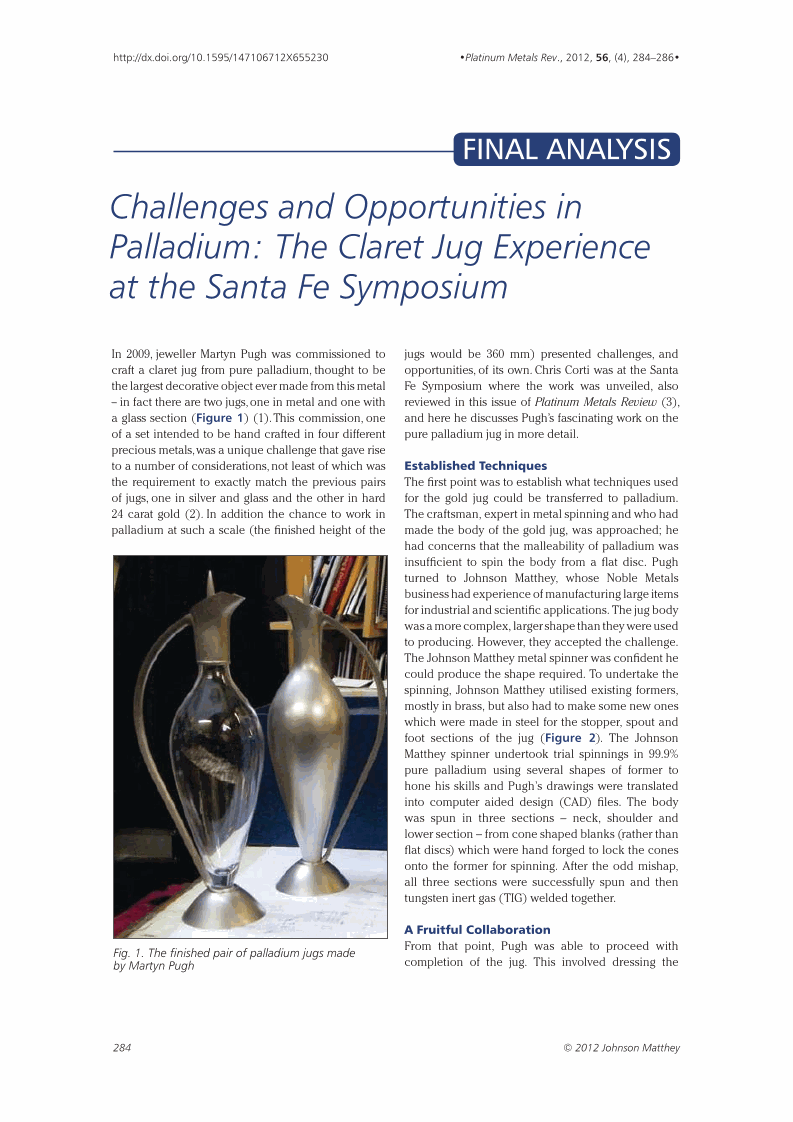



FINAL ANALYSIS: Challenges and Opportunities in Palladium: The Claret Jug Experience at the Santa Fe Symposium, Page 1 of 1
< Previous page Next page > /docserver/preview/fulltext/pmr/56/4/PMR-56-4-Corti-2-1.gif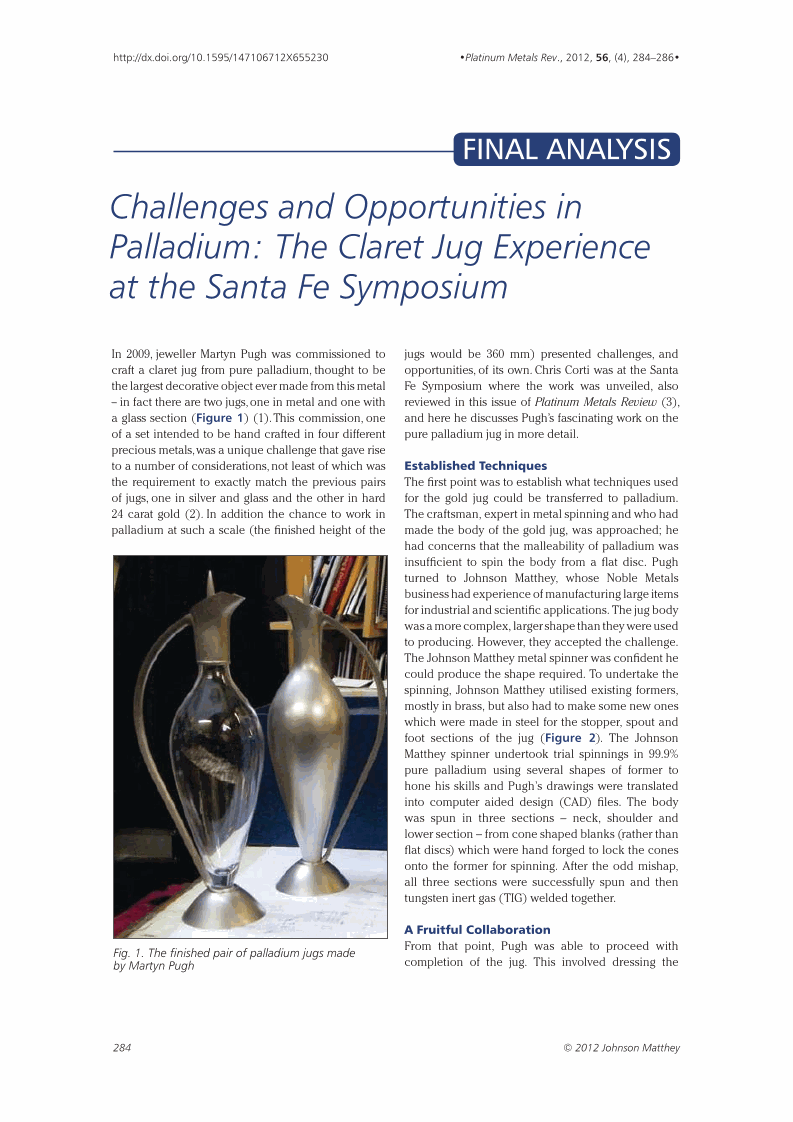
There is no abstract available.
© Johnson Matthey