-
oa Patents
- Source: Platinum Metals Review, Volume 57, Issue 2, Apr 2013, p. 154 - 156
-
- 01 Jan 2013
Preview this article:
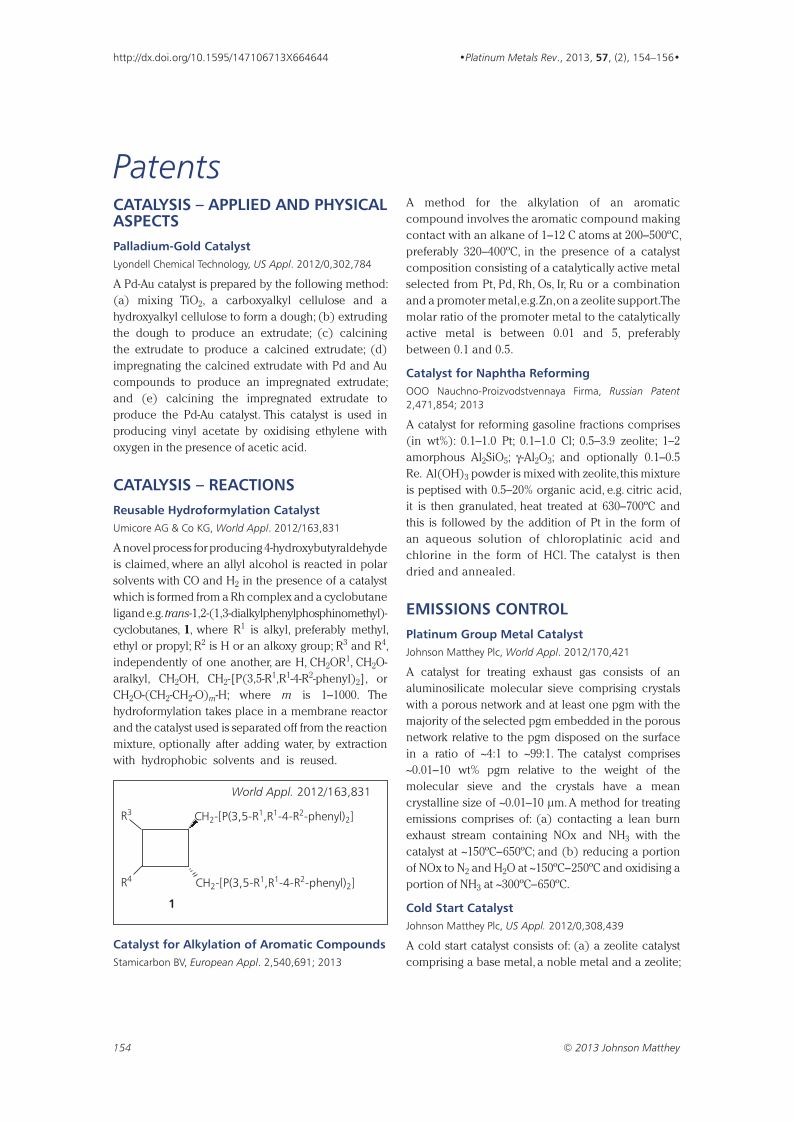



Patents, Page 1 of 1
< Previous page Next page > /docserver/preview/fulltext/pmr/57/2/JMTR-57-2-Patents-1.gif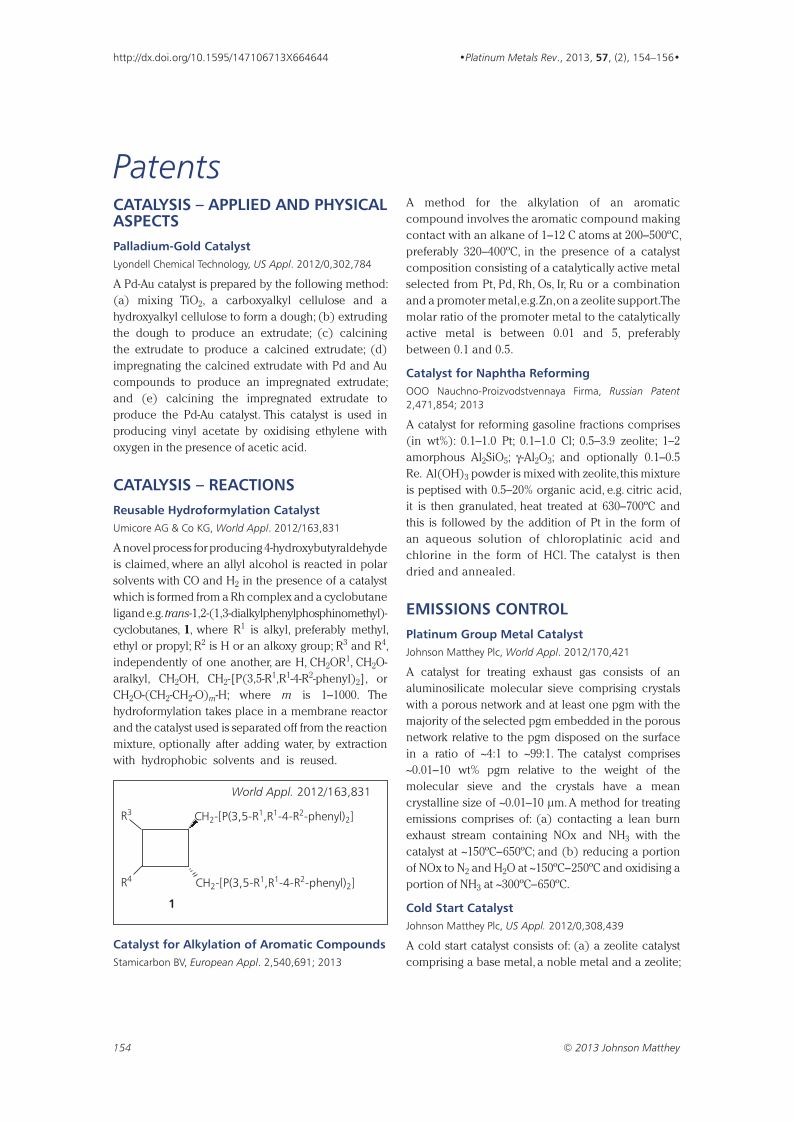
There is no abstract available.
© Johnson Matthey