-
oa Final Analysis: Effects of Platinum Group Metals Doping on Stainless Steels
- Source: Platinum Metals Review, Volume 58, Issue 1, Jan 2014, p. 54 - 57
-
- 01 Jan 2014
Preview this article:
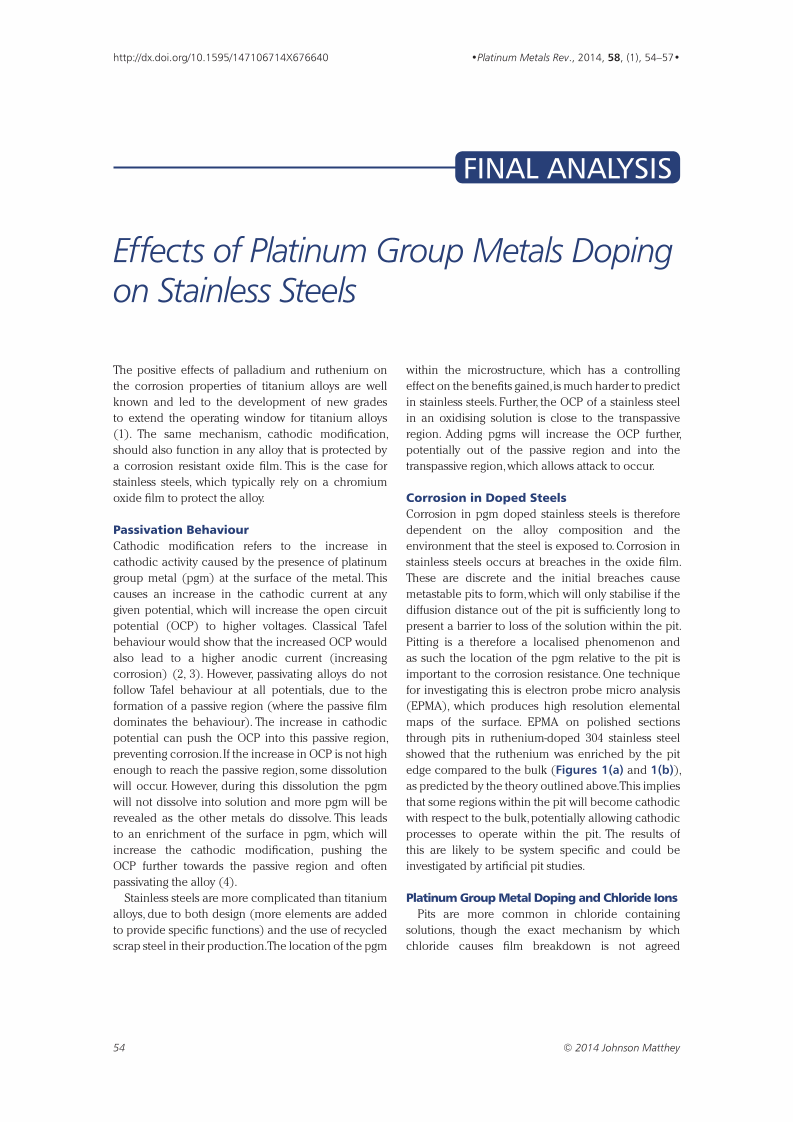



Final Analysis: Effects of Platinum Group Metals Doping on Stainless Steels, Page 1 of 1
< Previous page Next page > /docserver/preview/fulltext/pmr/58/1/PMR-58-1-Fones-1.gif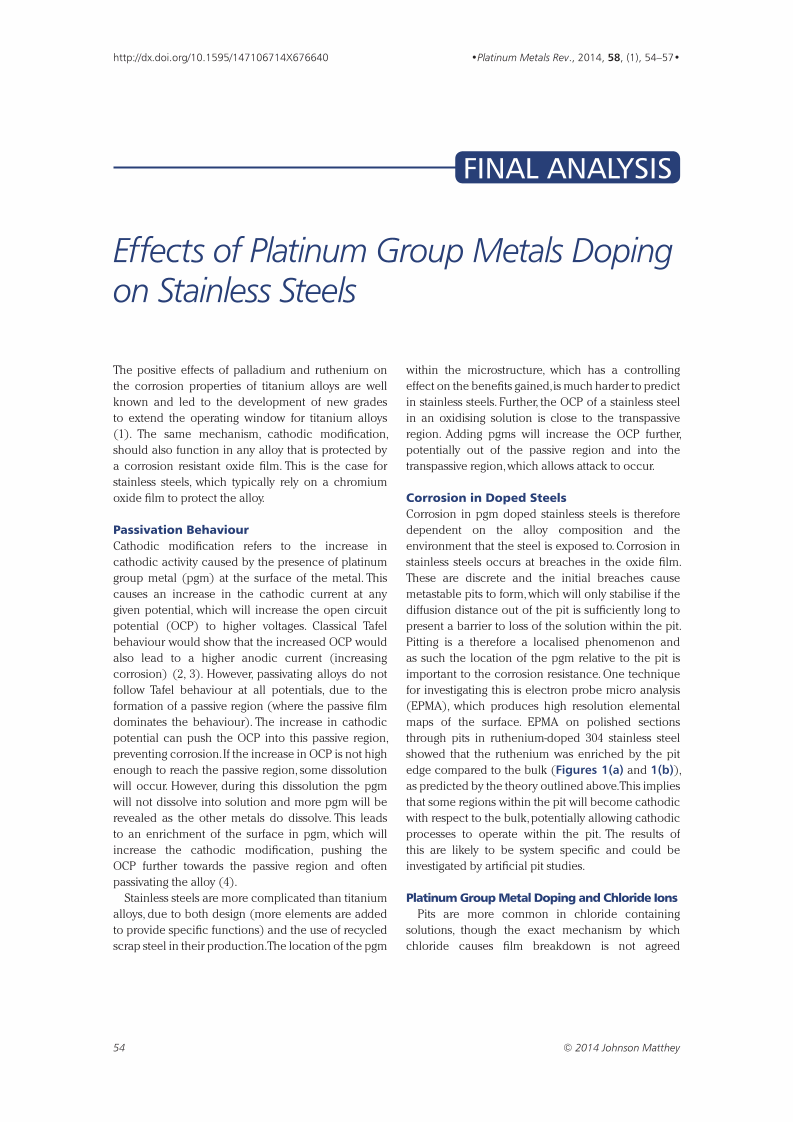
There is no abstract available.
© Johnson Matthey