-
oa The Generation of Pure Hydrogen for Industrial Applications
On-site Production Uses Silver-palladium Membranes
- Source: Platinum Metals Review, Volume 25, Issue 1, Jan 1981, p. 12 - 13
-
- 01 Jan 1981
Preview this article:
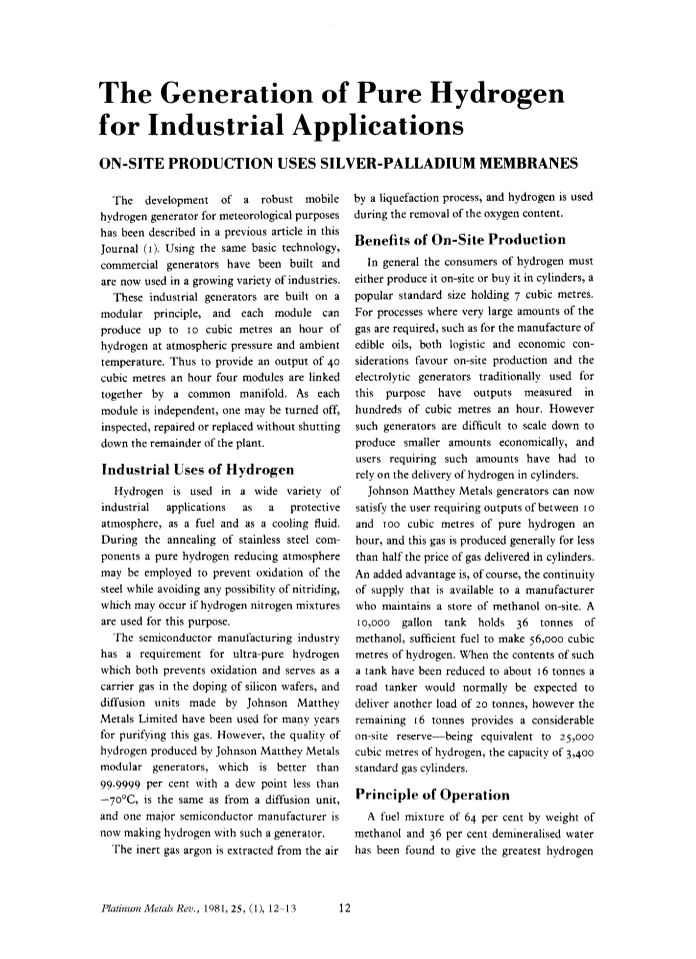



The Generation of Pure Hydrogen for Industrial Applications, Page 1 of 1
< Previous page Next page > /docserver/preview/fulltext/pmr/25/1/pmr0025-0012-1.gif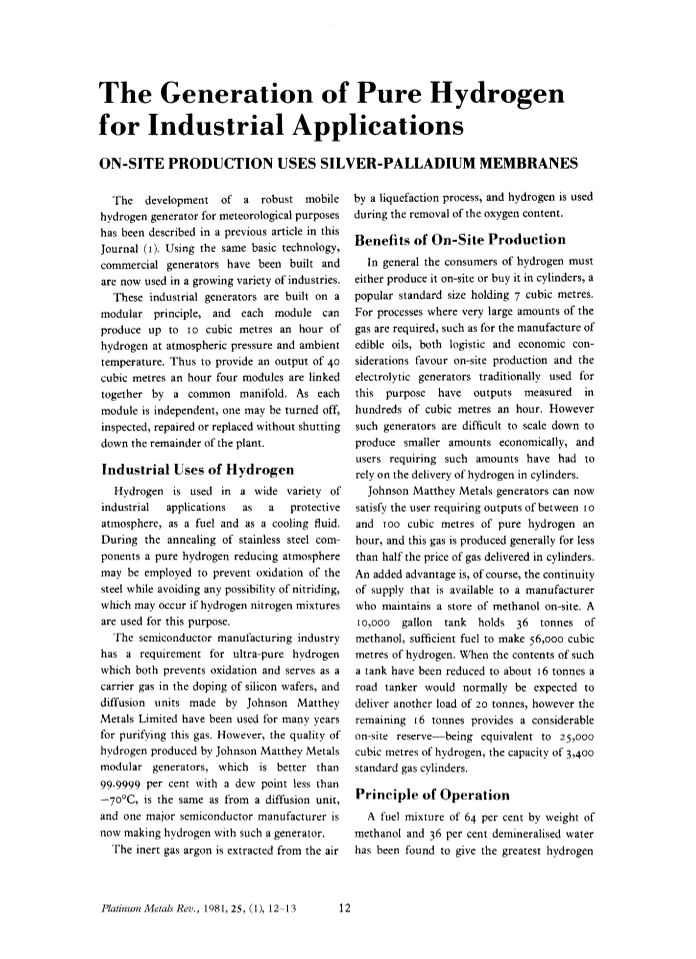
There is no abstract available.
© Johnson Matthey