-
oa Platinum Catalysts in Oil Refining
Studies of Reaction Mechanisms
- Source: Platinum Metals Review, Volume 26, Issue 1, Jan 1982, p. 19 - 19
-
- 01 Jan 1982
Preview this article:
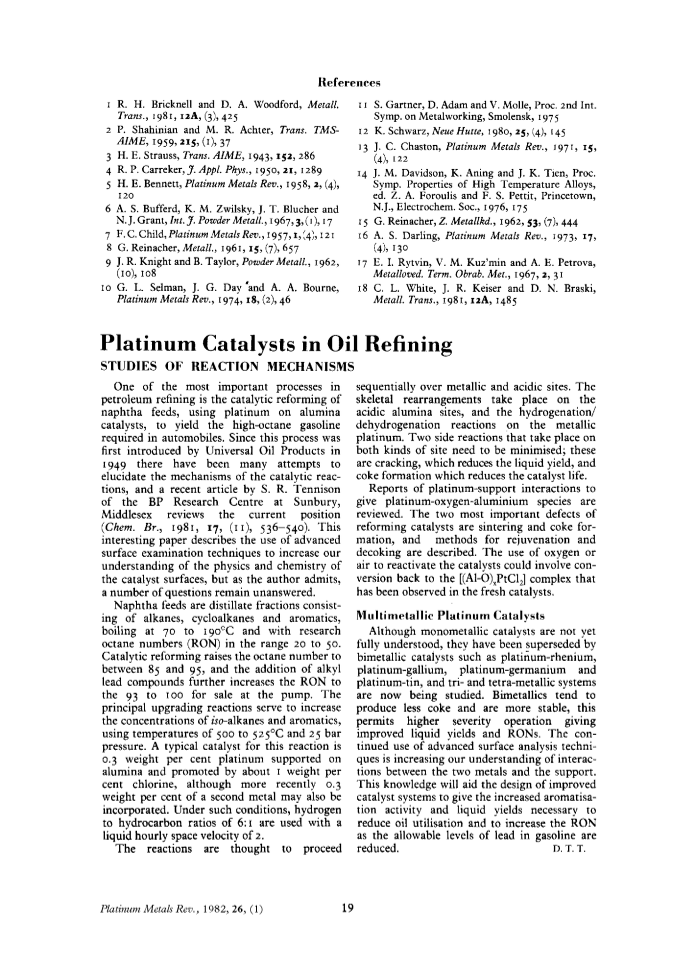



Platinum Catalysts in Oil Refining, Page 1 of 1
< Previous page Next page > /docserver/preview/fulltext/pmr/26/1/pmr0026-0019-1.gif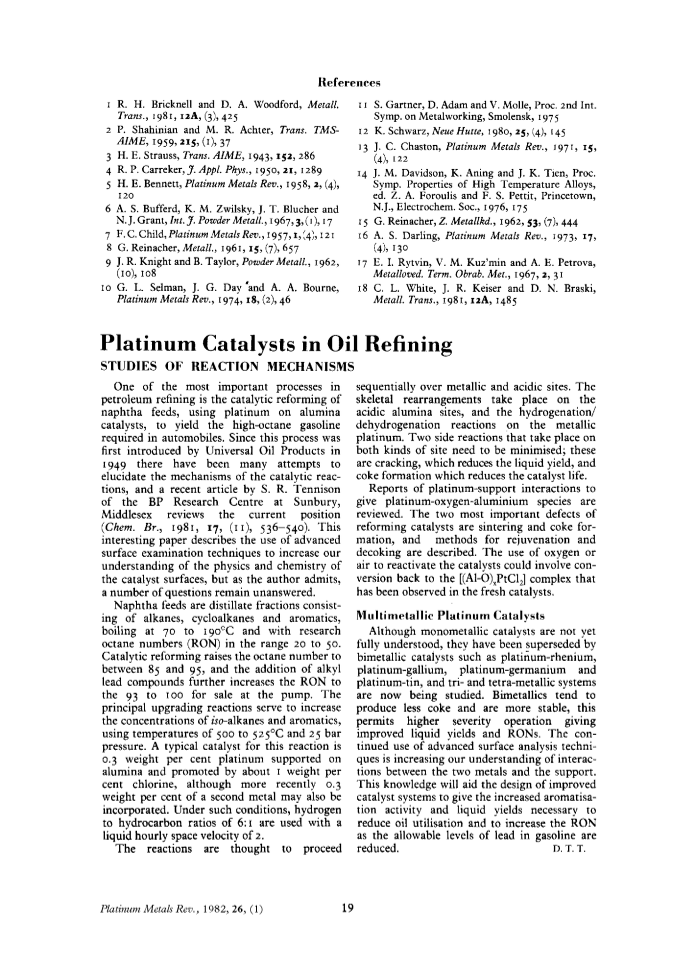
There is no abstract available.
© Johnson Matthey