-
oa The Recovery of Platinum from Ammonia Oxidation Catalysts
The Current State of the Catchment Gauze Process
- Source: Platinum Metals Review, Volume 26, Issue 1, Jan 1982, p. 28 - 32
-
- 01 Jan 1982
Preview this article:
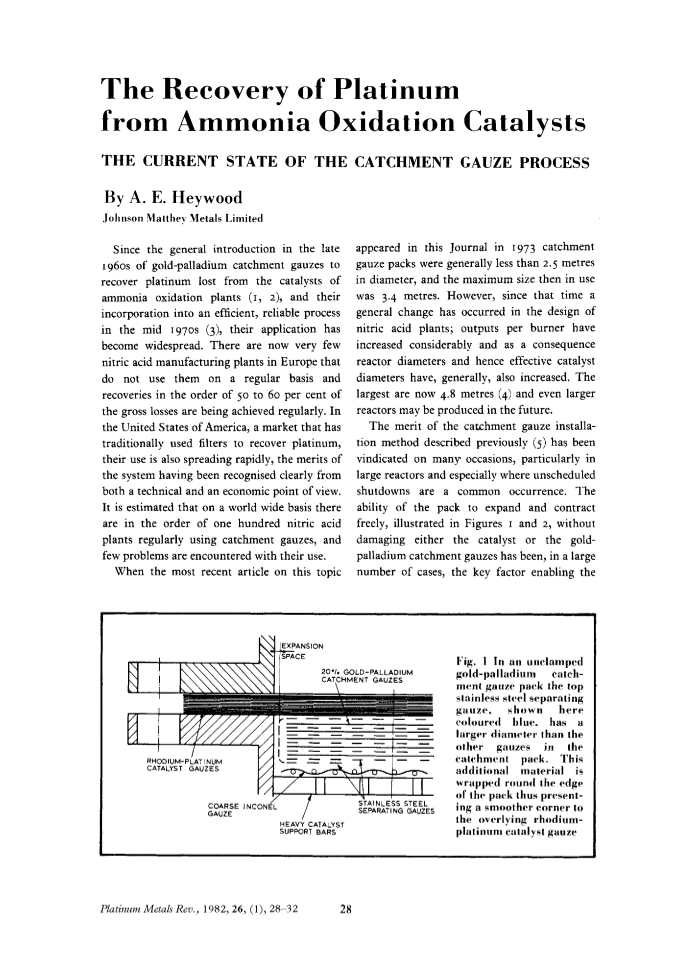



The Recovery of Platinum from Ammonia Oxidation Catalysts, Page 1 of 1
< Previous page Next page > /docserver/preview/fulltext/pmr/26/1/pmr0026-0028-1.gif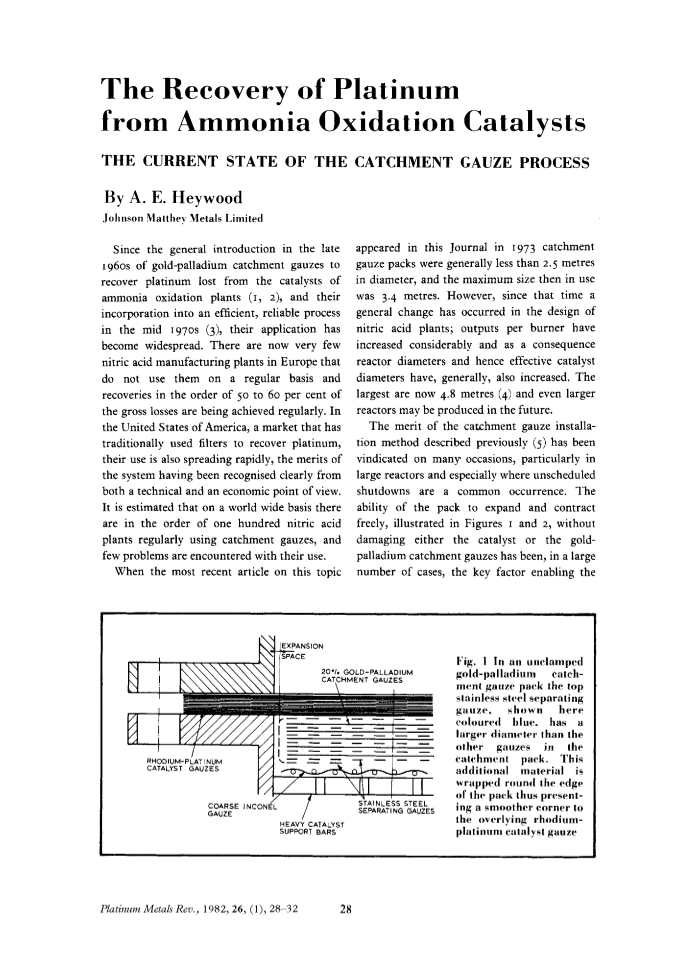
There is no abstract available.
© Johnson Matthey