-
oa New Solvent Extraction Plant Opened
Platinum Refinery Expanded and Modernised
- Source: Platinum Metals Review, Volume 27, Issue 3, Jul 1983, p. 110 - 110
-
- 01 Jan 1983
Preview this article:
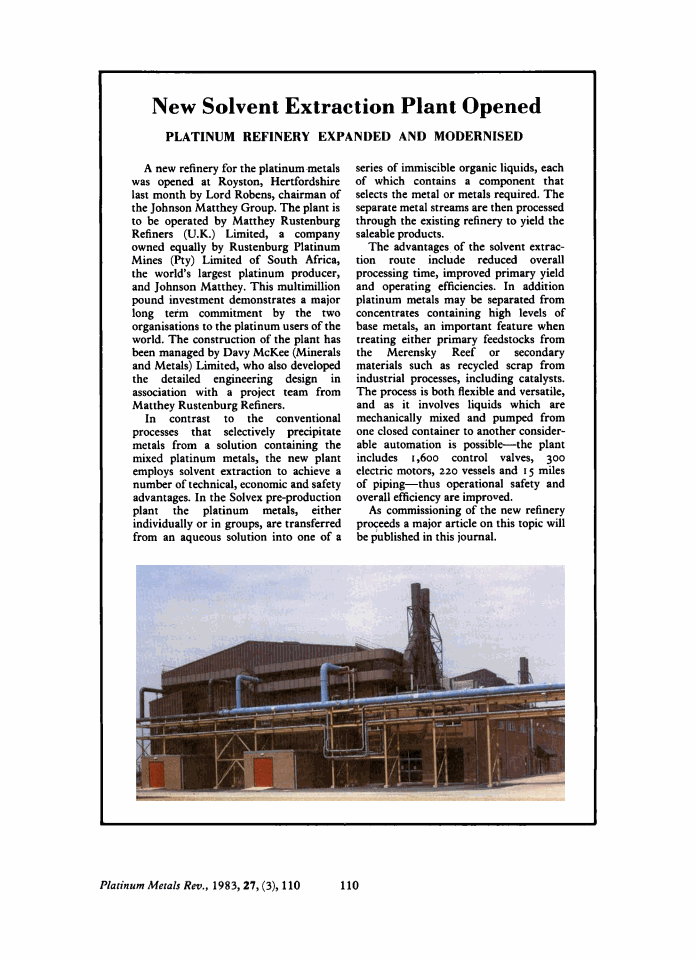



New Solvent Extraction Plant Opened, Page 1 of 1
< Previous page Next page > /docserver/preview/fulltext/pmr/27/3/pmr0027-0110-1.gif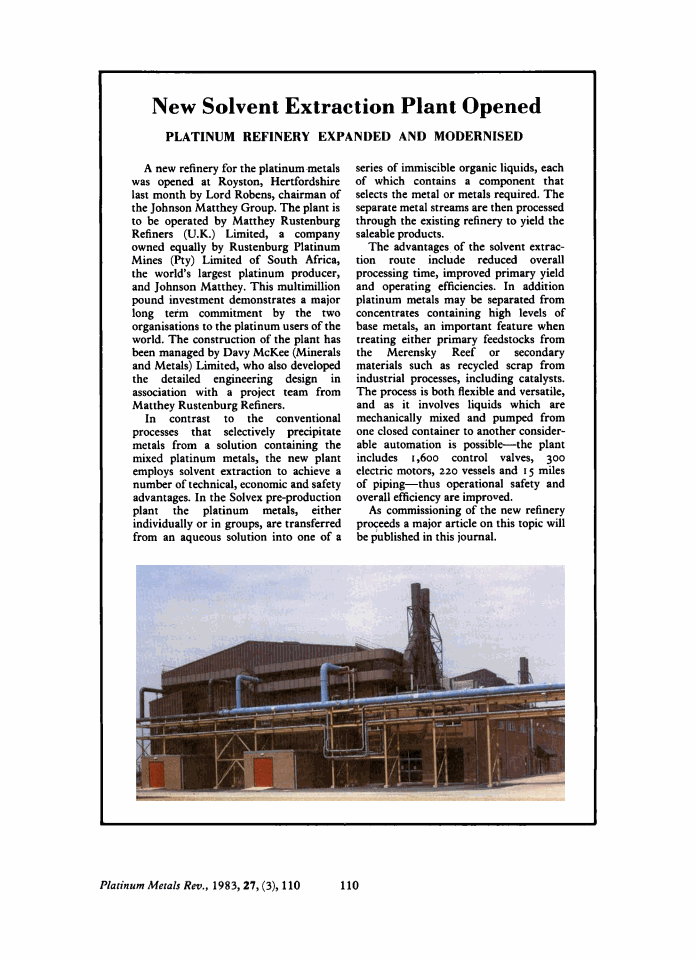
There is no abstract available.
© Johnson Matthey