-
oa Automotive Exhaust Emissions Control
- Source: Platinum Metals Review, Volume 47, Issue 4, Oct 2003, p. 157 - 162
-
- 01 Jan 2003
Preview this article:
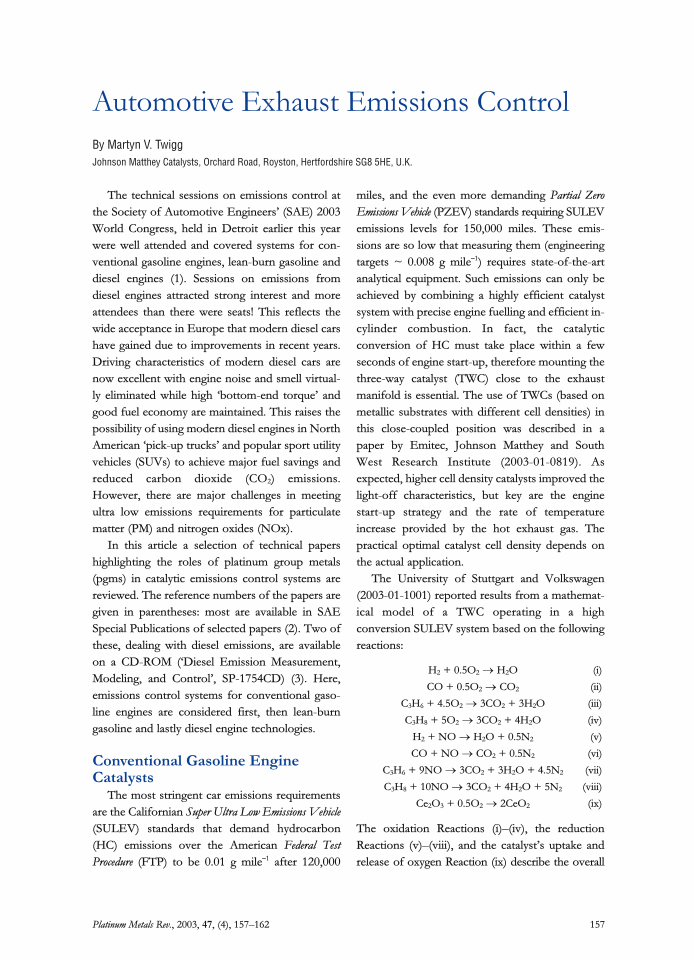



Automotive Exhaust Emissions Control, Page 1 of 1
< Previous page Next page > /docserver/preview/fulltext/pmr/47/4/pmr0047-0157-1.gif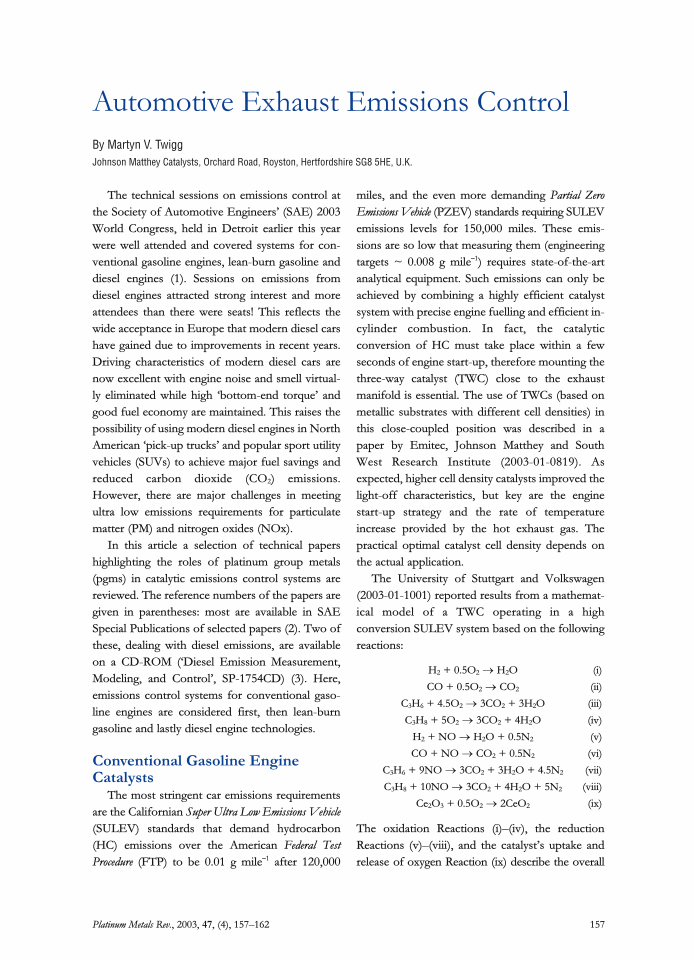
There is no abstract available.
© Johnson Matthey