-
oa The Tenth Grove Fuel Cell Symposium
FUEL CELLS IN A CHANGING WORLD – A PROGRESS REPORT
- Source: Platinum Metals Review, Volume 52, Issue 1, Jan 2008, p. 12 - 20
-
- 01 Jan 2008
Preview this article:
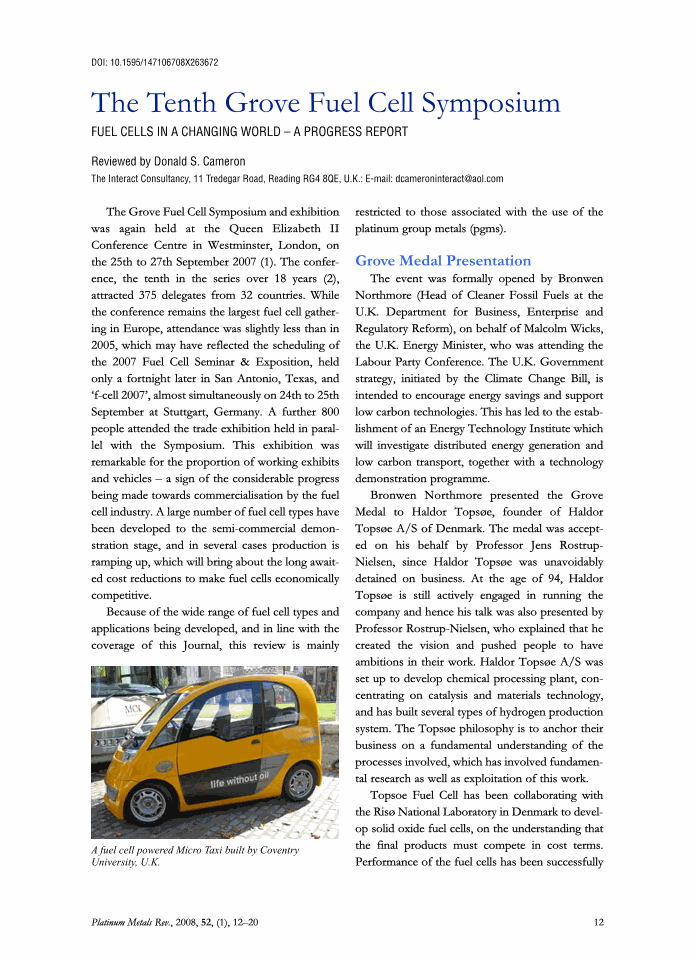



The Tenth Grove Fuel Cell Symposium, Page 1 of 1
< Previous page Next page > /docserver/preview/fulltext/pmr/52/1/PMR-52-1-Cameron-1.gif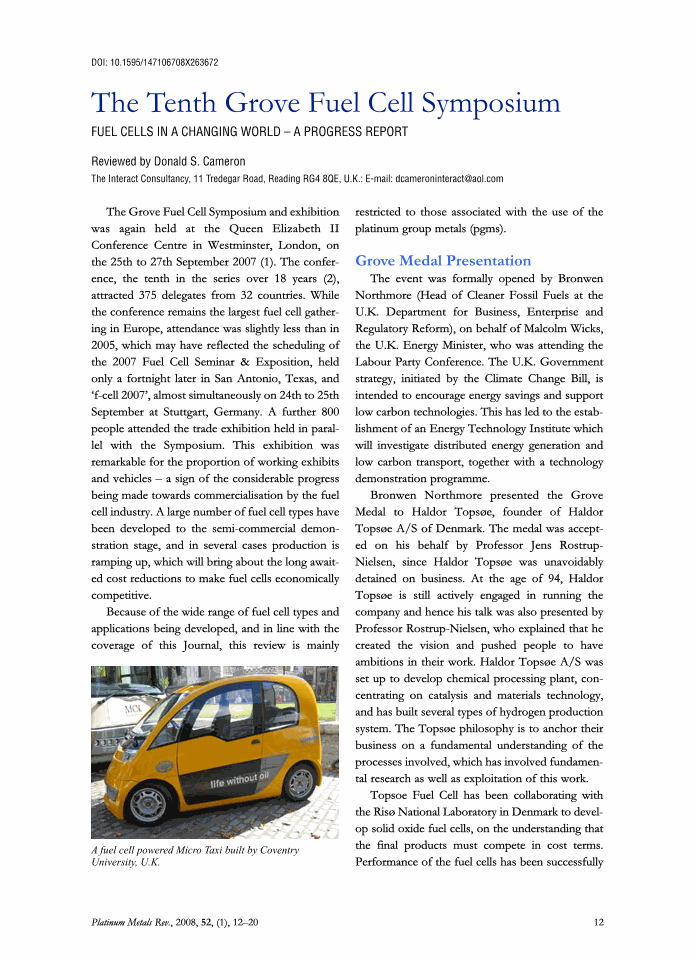
There is no abstract available.
© Johnson Matthey