-
oa Platinum Group Metal Catalysed Hydrodeoxygenation Of Model Bio-oil Compounds
Investigating catalysts for upgrading bio-oils to fuels and chemicals
- Source: Johnson Matthey Technology Review, Volume 58, Issue 3, Jul 2014, p. 156 - 161
-
- 01 Jan 2014
Preview this article:
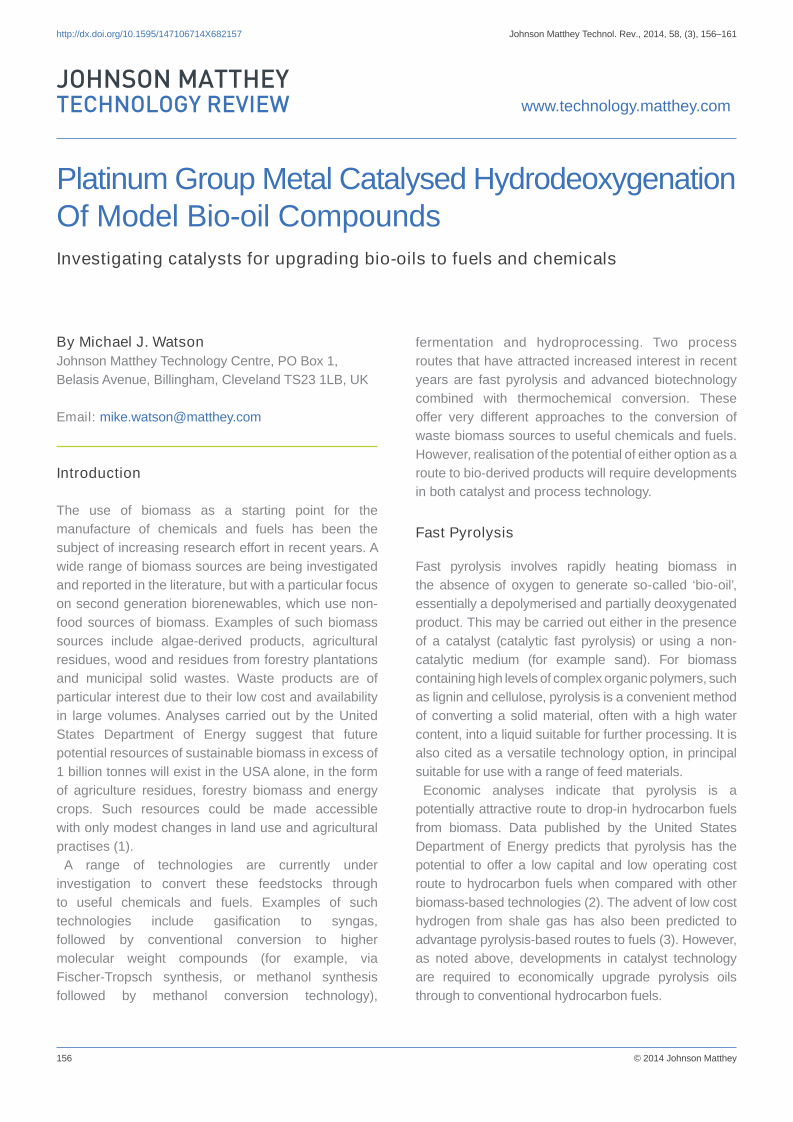



Platinum Group Metal Catalysed Hydrodeoxygenation Of Model Bio-oil Compounds, Page 1 of 1
< Previous page Next page > /docserver/preview/fulltext/jmtr/58/3/JMTR-58-03-Watson-1.gif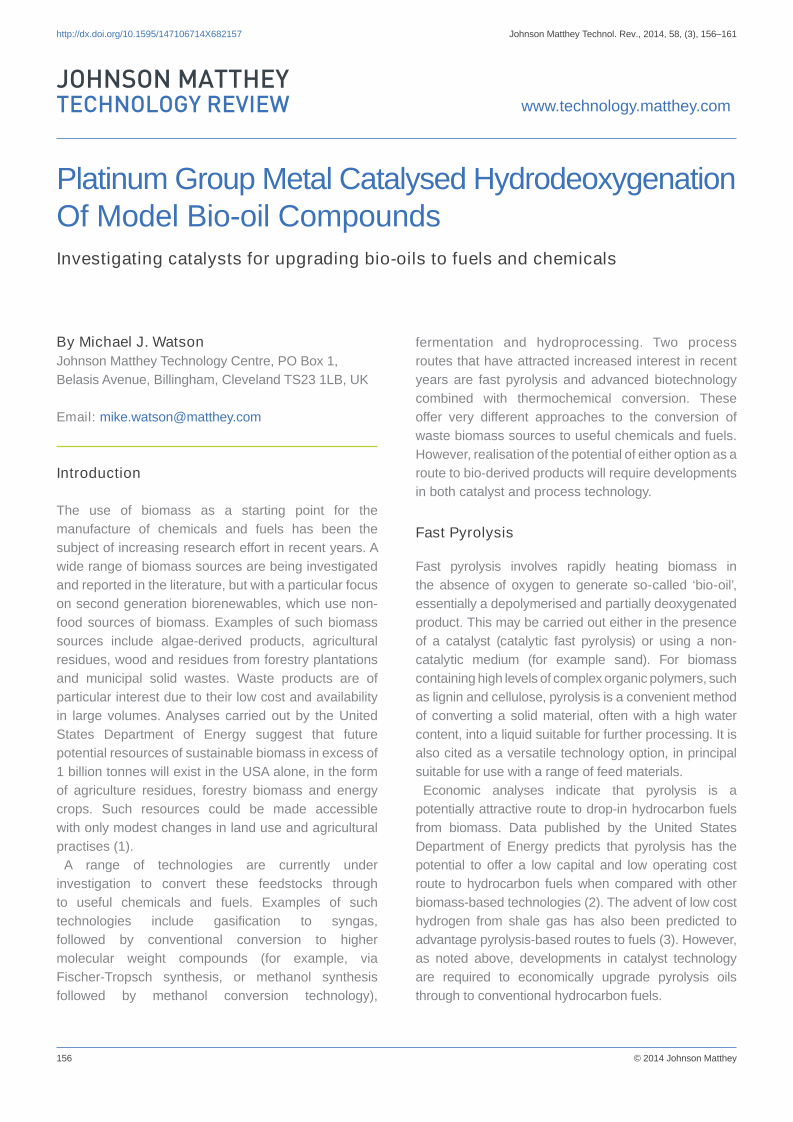
There is no abstract available.
© Johnson Matthey