-
oa The 28th Santa Fe Symposium on Jewelry Manufacturing Technology
Better understanding of lost wax casting of platinum leading to improved casting alloys
- Source: Johnson Matthey Technology Review, Volume 58, Issue 4, Oct 2014, p. 189 - 194
-
- 01 Jan 2014
Preview this article:
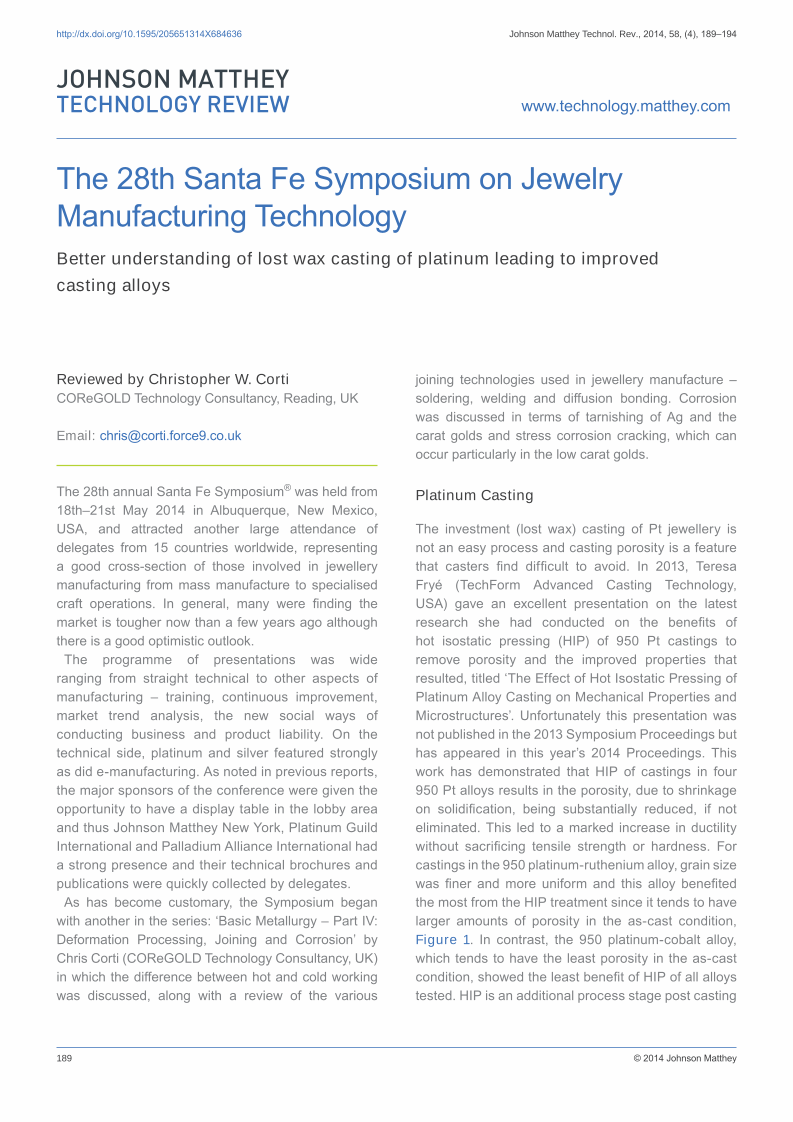



The 28th Santa Fe Symposium on Jewelry Manufacturing Technology, Page 1 of 1
< Previous page Next page > /docserver/preview/fulltext/jmtr/58/4/JMTR-58-4-Corti-1.gif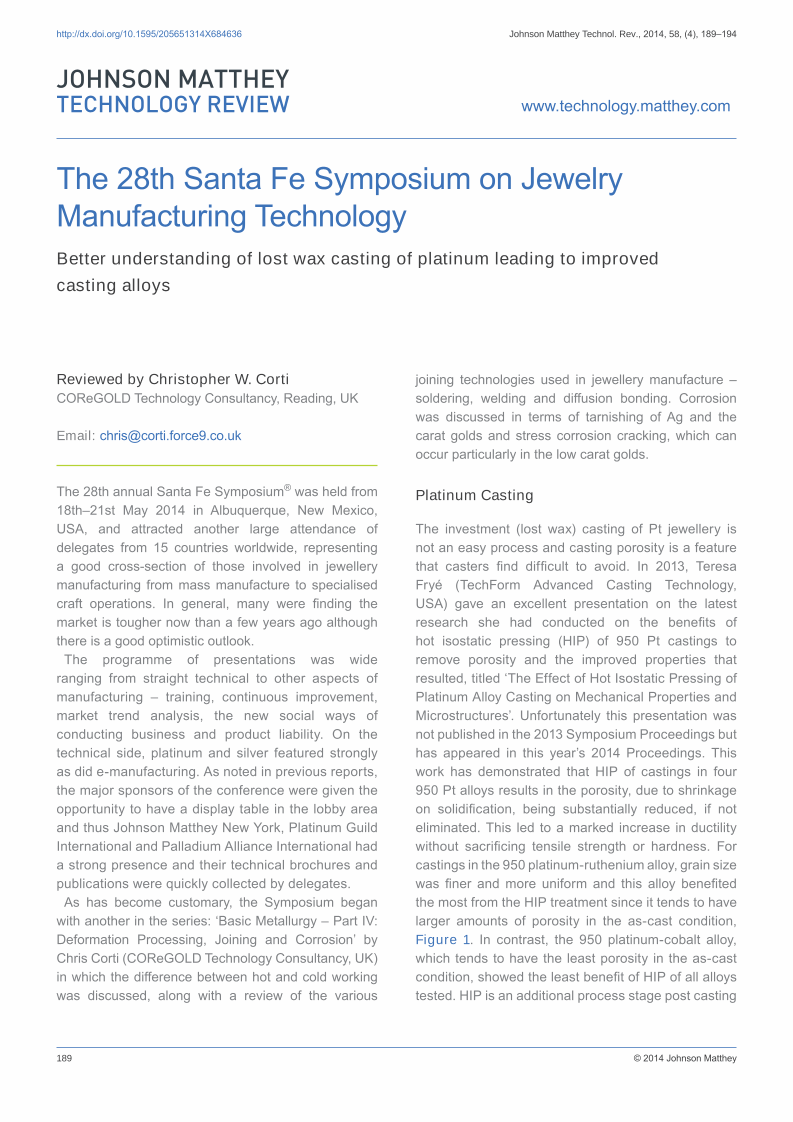
There is no abstract available.
© Johnson Matthey