-
oa Platinum Group Metal and Washcoat Chemistry Effects on Coated Gasoline Particulate Filter Design
Development of gasoline particulate filters to meet Euro 6c
- Source: Johnson Matthey Technology Review, Volume 59, Issue 3, Apr 2015, p. 188 - 192
Preview this article:
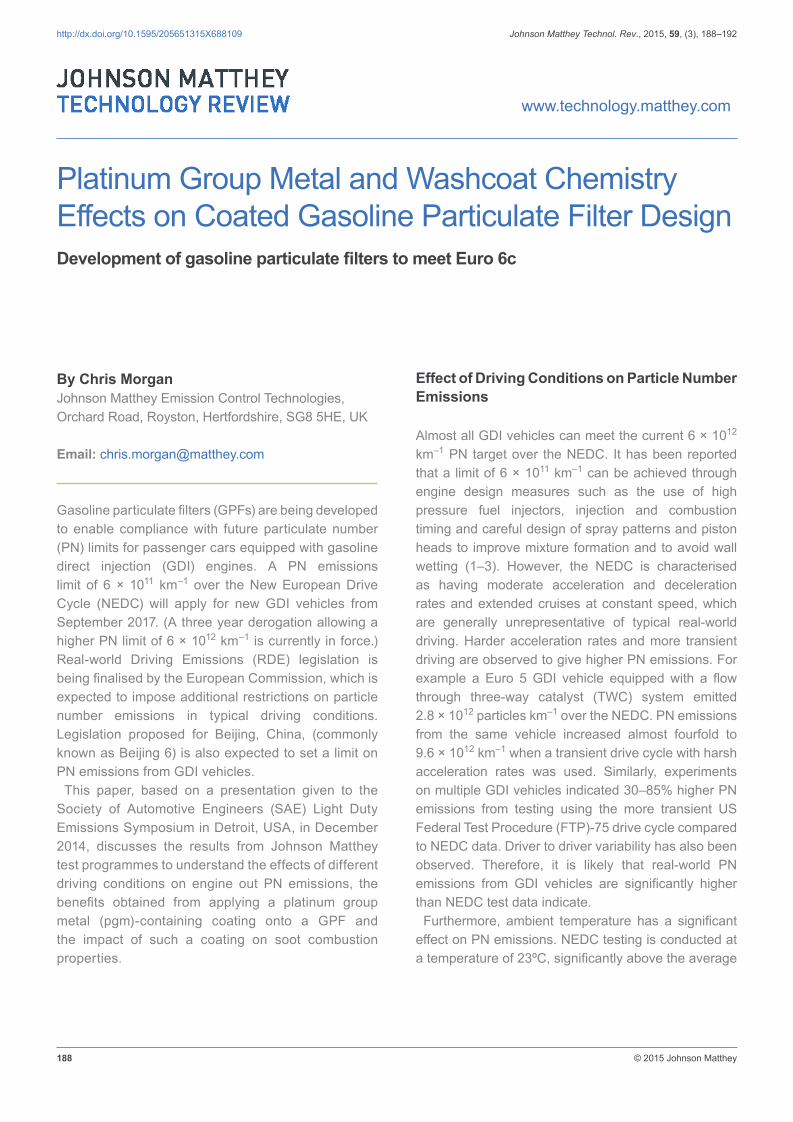



Platinum Group Metal and Washcoat Chemistry Effects on Coated Gasoline Particulate Filter Design, Page 1 of 1
< Previous page Next page > /docserver/preview/fulltext/jmtr/59/3/JMTR-59-3-Morgan-1.gif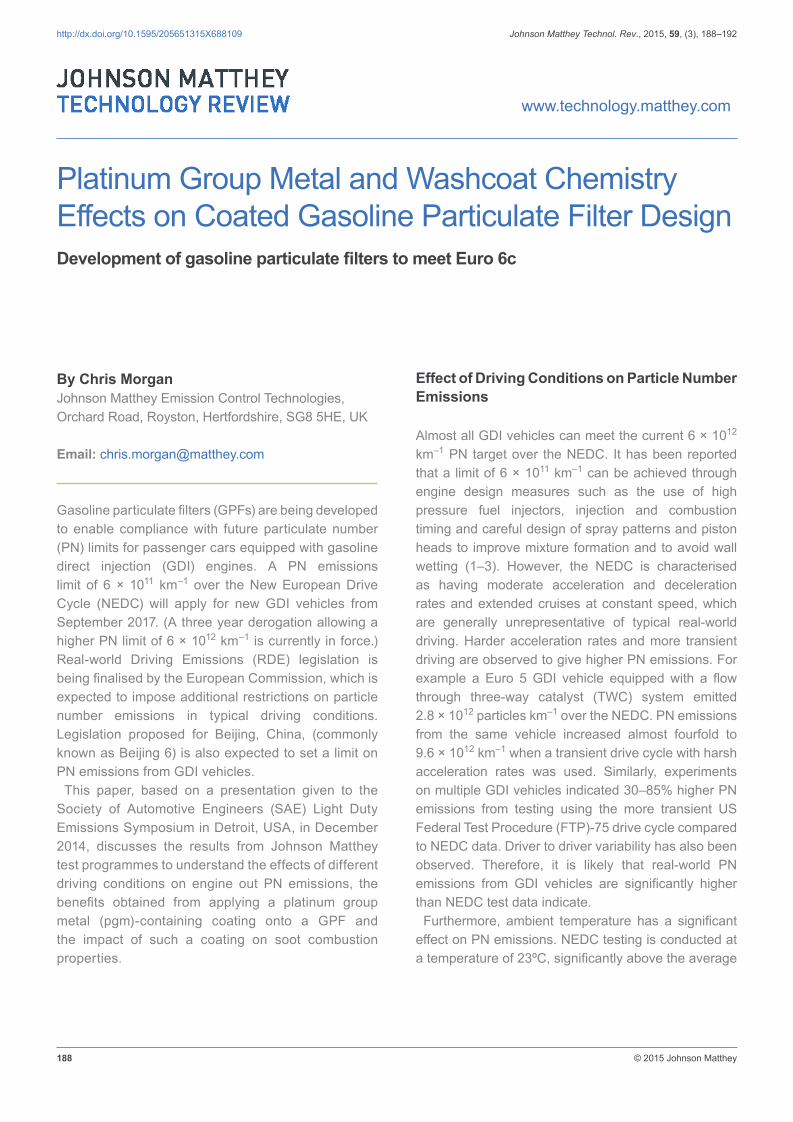
There is no abstract available.
© 2015 Johnson Matthey
This is an Open Access article distributed in accordance with the Creative Commons Attribution Non Commercial (CC BY-NC 4.0) license, which permits others to distribute, remix, adapt, build upon this work non-commercially, and license their derivative works on different terms, provided the original work is properly cited and the use is non-commercial. See: http://creativecommons.org/licenses/by-nc/4.0/