-
oa “Hierarchical Nanostructures for Energy Devices”
Edited by Seung Hwan Ko (Seoul National University, Korea) and Costas P. Grigoropoulos (University of California, Berkeley, USA), RSC Nanoscience & Nanotechnology Series, No. 35, Royal Society of Chemistry, Cambridge, UK, 2015, 308 pages, ISBN: 978-1-84973-628-2, £165.00, US$270.00, €206.25
- Source: Johnson Matthey Technology Review, Volume 60, Issue 2, Apr 2016, p. 151 - 157
-
- 01 Jan 2016
Preview this article:
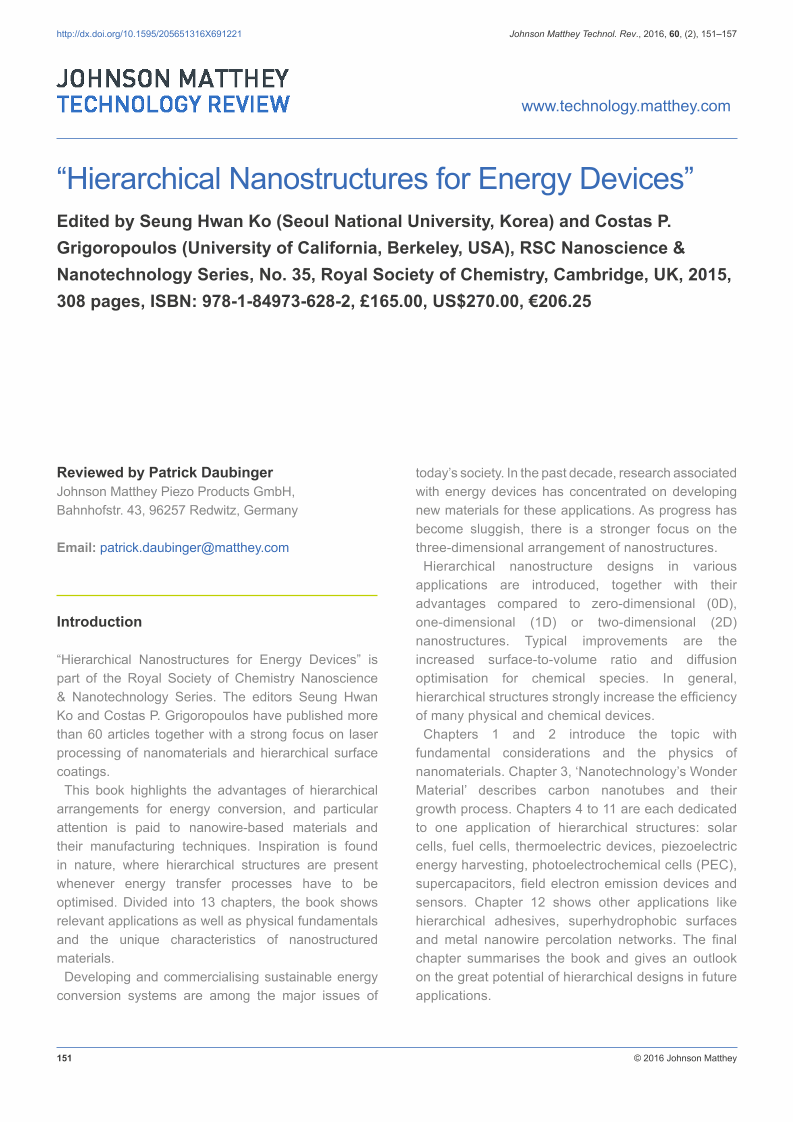



“Hierarchical Nanostructures for Energy Devices”, Page 1 of 1
< Previous page Next page > /docserver/preview/fulltext/jmtr/60/2/JMTR-60-2-Daubinger-1.gif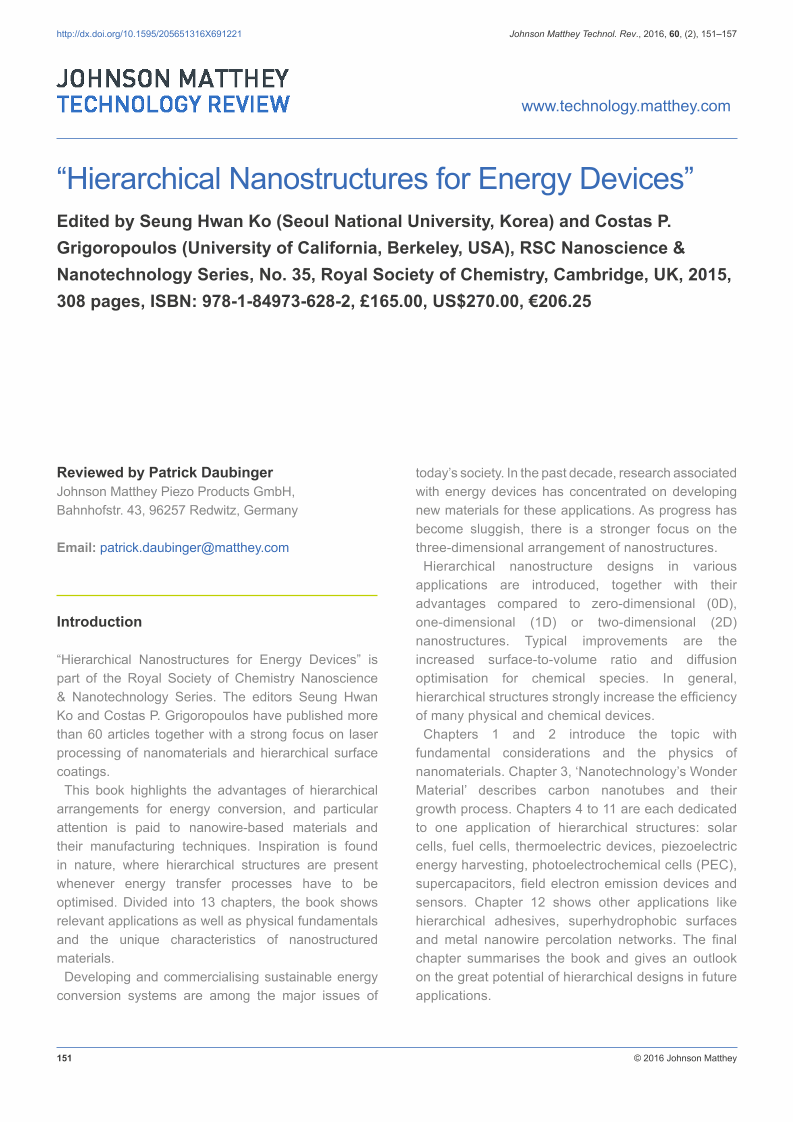
There is no abstract available.
© Johnson Matthey