-
oa Durability and Degradation Issues in PEM Electrolysis Cells and its Components
The second international workshop organised by the NOVEL EU-funded programme
- Source: Johnson Matthey Technology Review, Volume 61, Issue 1, Jan 2017, p. 47 - 51
-
- 01 Jan 2017
Preview this article:
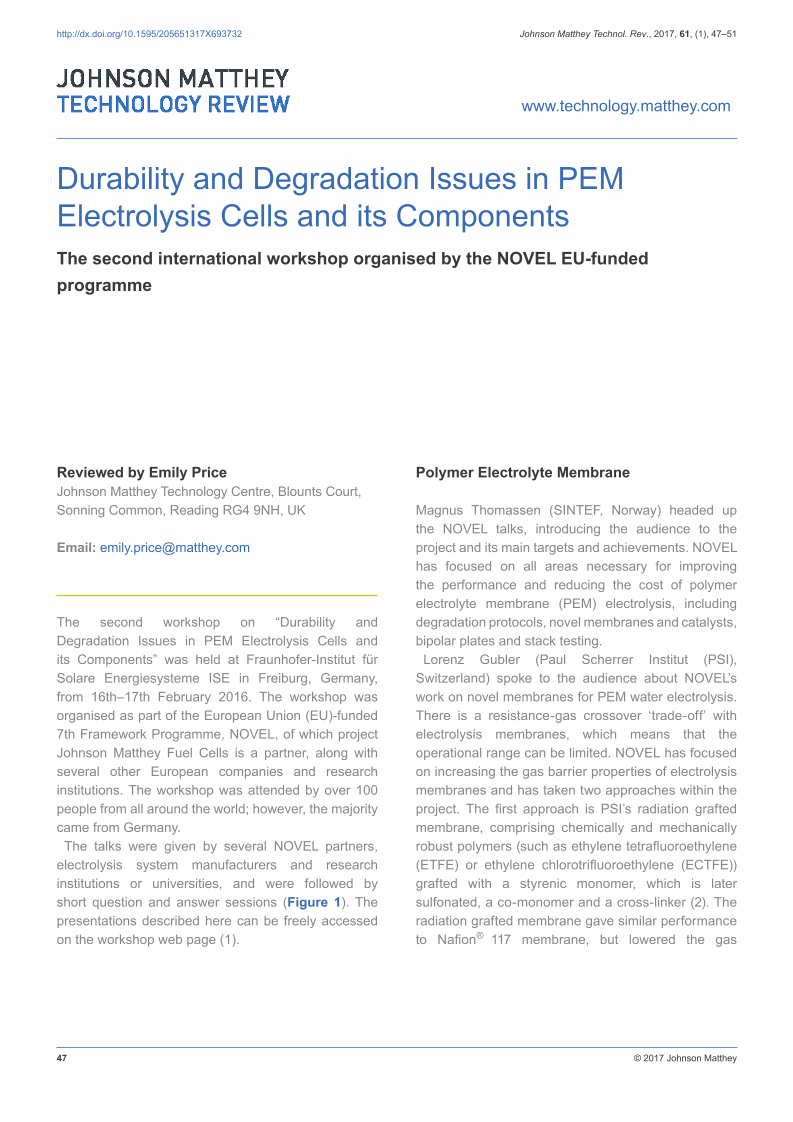



Durability and Degradation Issues in PEM Electrolysis Cells and its Components, Page 1 of 1
< Previous page Next page > /docserver/preview/fulltext/jmtr/61/1/JMTR-61-1-Price-1.gif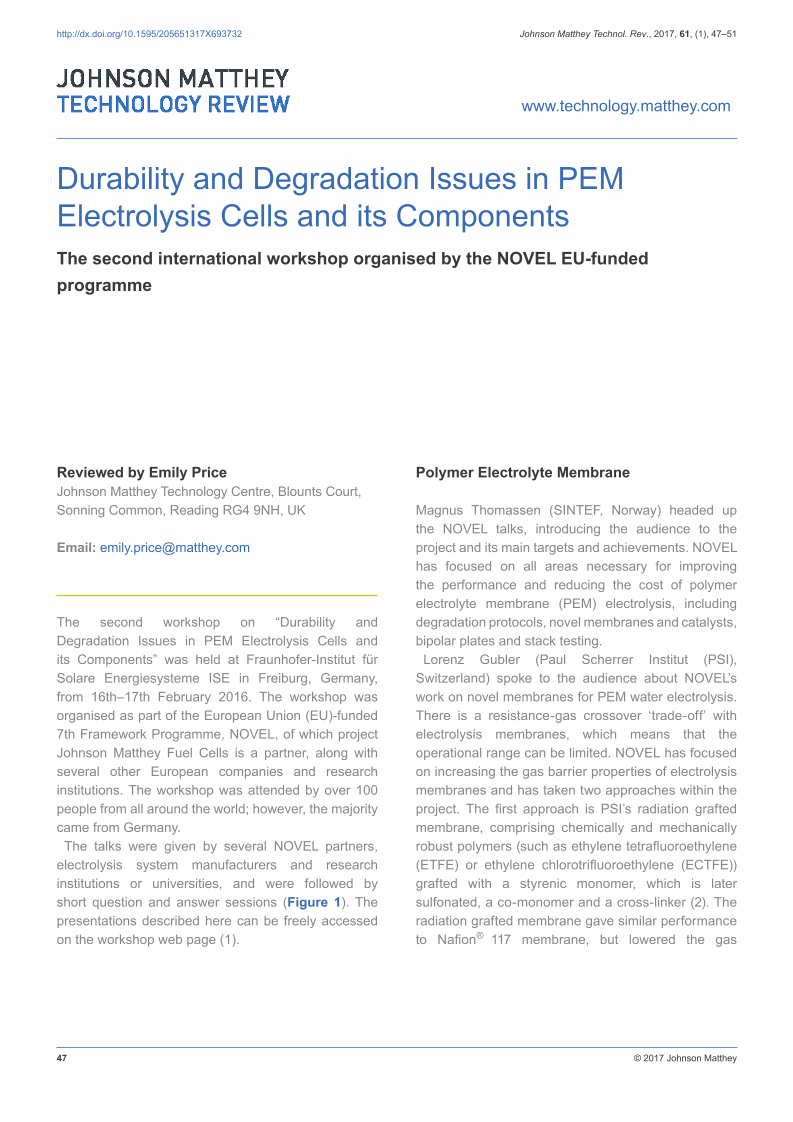
There is no abstract available.
© Johnson Matthey