-
oa “Palladium Membrane Technology for Hydrogen Production, Carbon Capture and Other Applications”
Edited by Aggelos Doukelis (National Technical University of Athens, Greece), Kyriakos Panopoulos (Chemical Process and Energy Resources Institute, Greece), Antonios Koumanakos and Emmanouil Kakaras (National Technical University of Athens, Greece), Woodhead Publishing, an imprint of Elsevier, Cambridge, UK, 2015, 383 pages, ISBN: 978-1-78242-234-1, £170.00, US$280.00
- Source: Johnson Matthey Technology Review, Volume 60, Issue 3, Jun 2016, p. 190 - 195
-
- 01 Jan 2016
Preview this article:
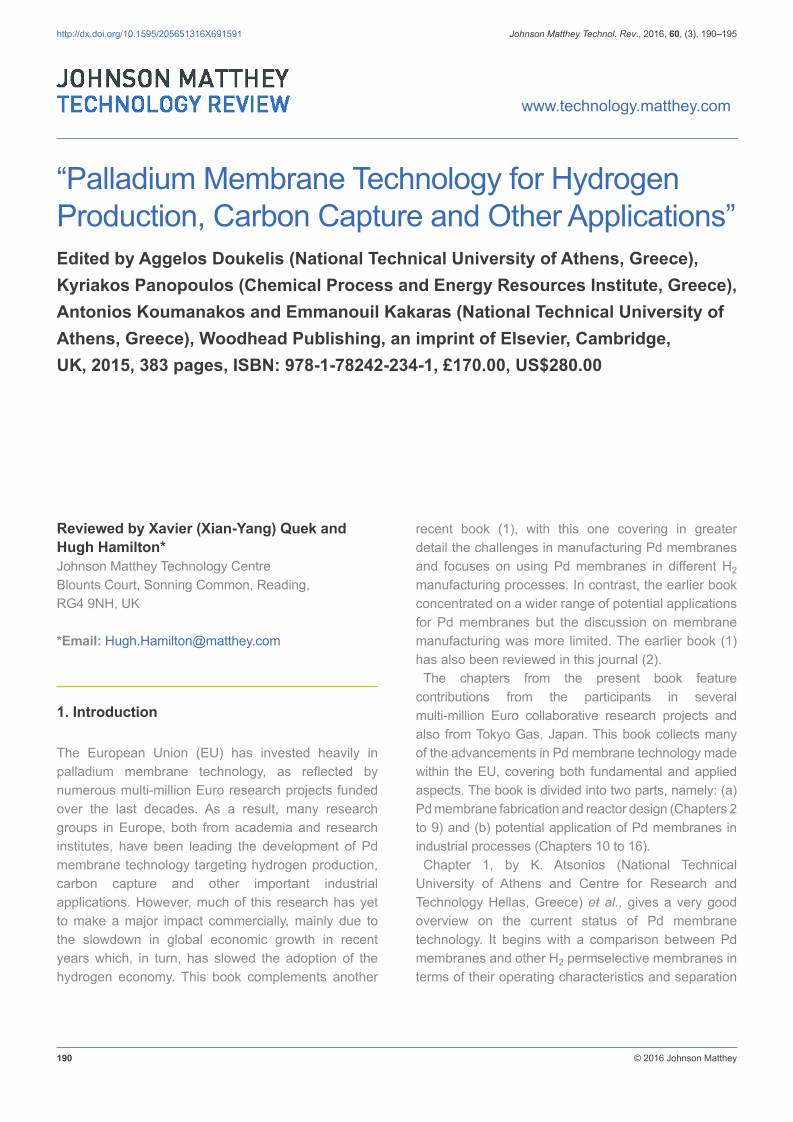



“Palladium Membrane Technology for Hydrogen Production, Carbon Capture and Other Applications”, Page 1 of 1
< Previous page Next page > /docserver/preview/fulltext/jmtr/60/3/JMTR-60-3-Hamilton-1.gif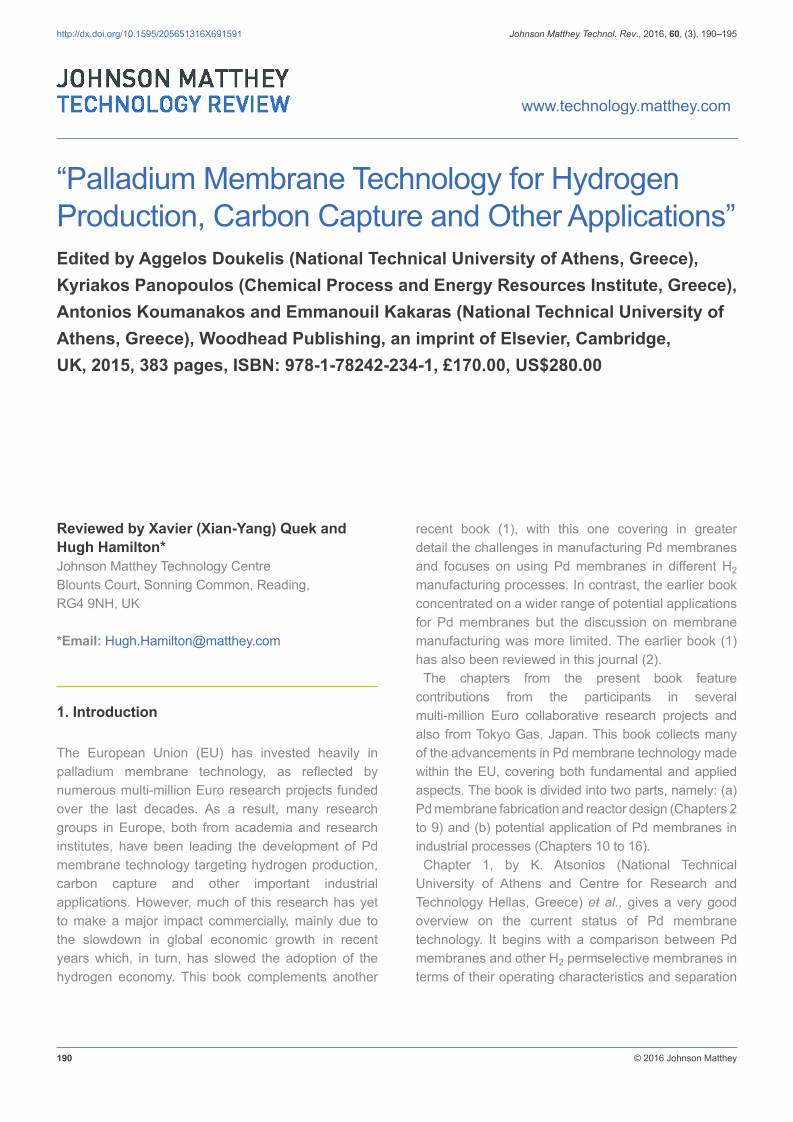
There is no abstract available.
© Johnson Matthey