-
oa “Particle Technology and Engineering: An Engineer’s Guide to Particles and Powders: Fundamentals and Computational Approaches”
By Jonathan Seville and Chuan-Yu Wu (University of Surrey, UK), Butterworth-Heinemann, an imprint of Elsevier, Oxford, UK, 2016, 294 pages, ISBN: 978-0-08-098337-0, £51.10, US$84.00, €60.16
- Source: Johnson Matthey Technology Review, Volume 61, Issue 3, Jul 2017, p. 227 - 230
-
- 01 Jan 2017
Preview this article:
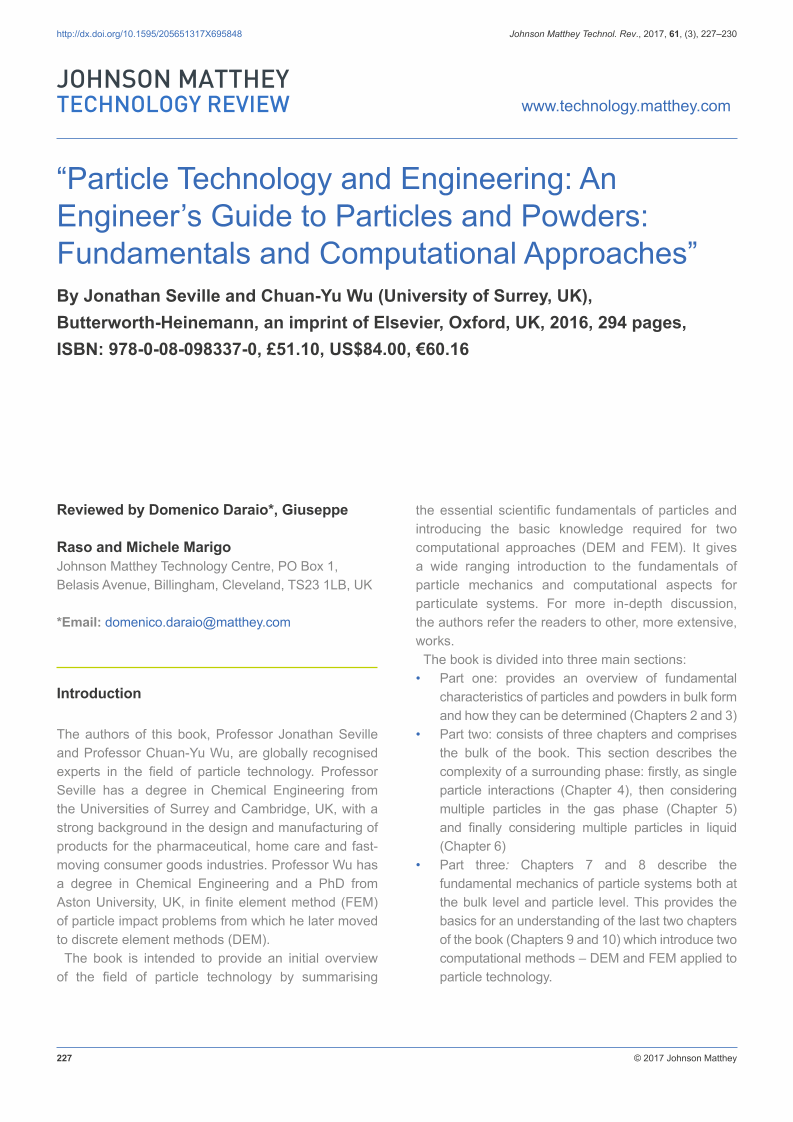



“Particle Technology and Engineering: An Engineer’s Guide to Particles and Powders: Fundamentals and Computational Approaches”, Page 1 of 1
< Previous page Next page > /docserver/preview/fulltext/jmtr/61/3/JMTR-61-3-Marigo-1.gif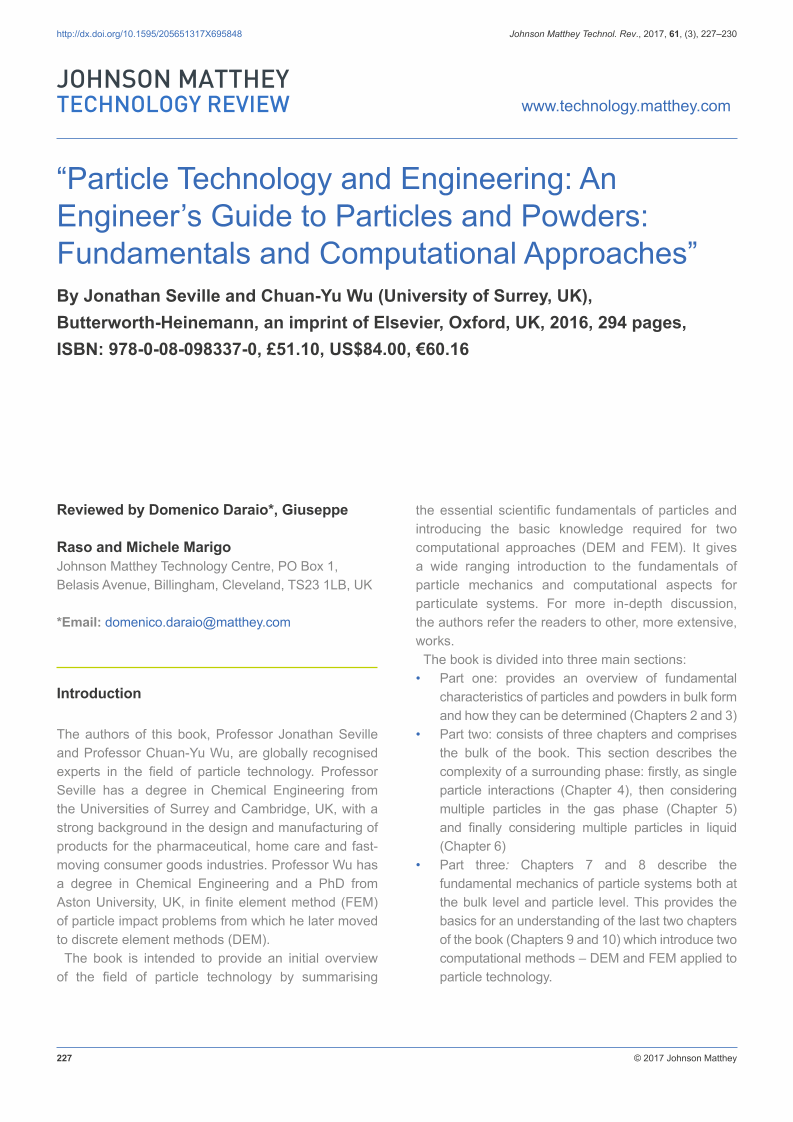
There is no abstract available.
© Johnson Matthey