-
oa In the Lab: Alternative Recycling Process for Lithium-ion Batteries: Molten Salt Approach
Johnson Matthey Technology Review features new laboratory research
- Source: Johnson Matthey Technology Review, Volume 64, Issue 1, Jan 2020, p. 16 - 18
-
- 01 Jan 2020
Preview this article:
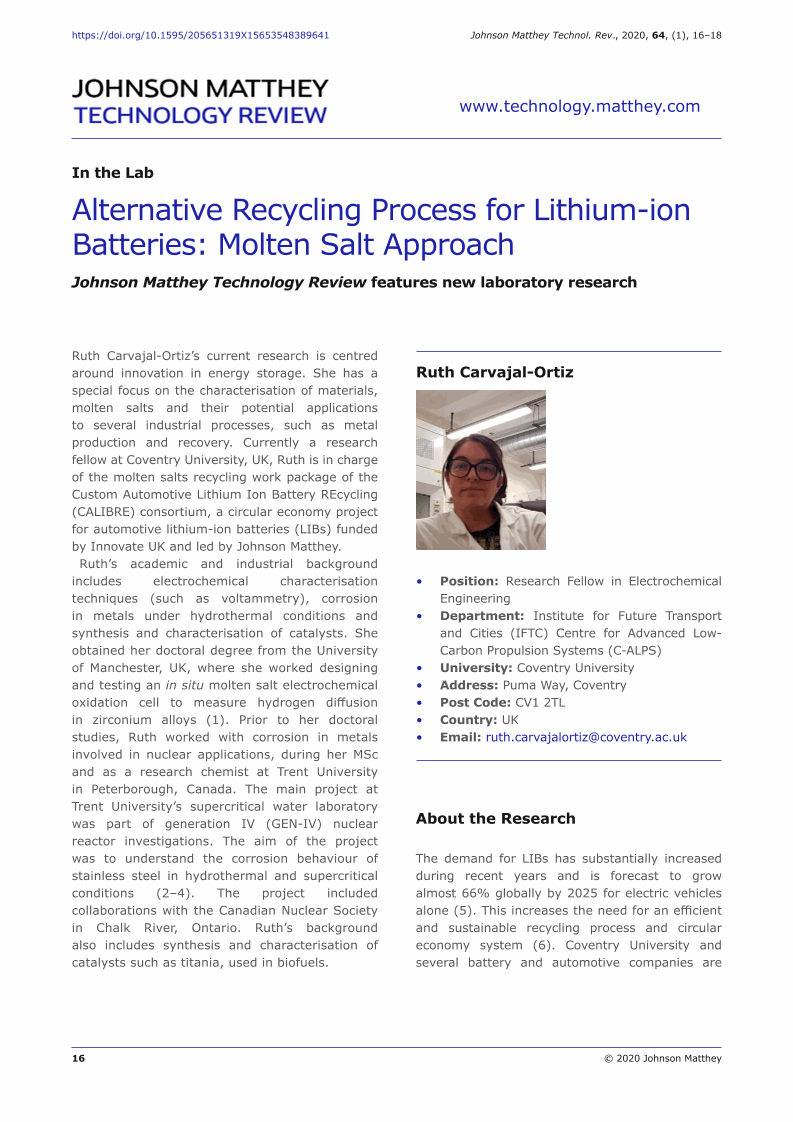



In the Lab: Alternative Recycling Process for Lithium-ion Batteries: Molten Salt Approach, Page 1 of 1
< Previous page Next page > /docserver/preview/fulltext/jmtr/64/1/Ortiz_16a_Imp-1.gif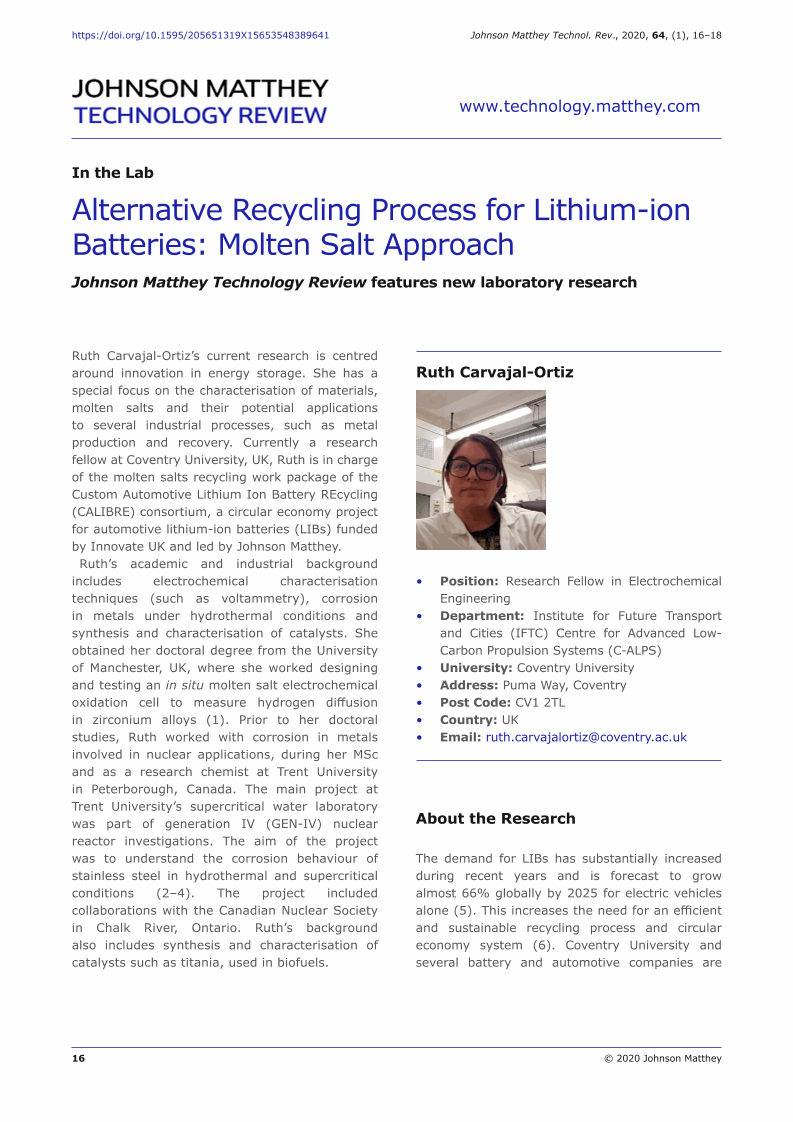
There is no abstract available.
© Johnson Matthey