-
oa Nanosurfaces 2019
Commercialised techniques involving plasma, surface coatings and graphene
- Source: Johnson Matthey Technology Review, Volume 64, Issue 2, Apr 2020, p. 148 - 151
-
- 01 Jan 2020
Preview this article:
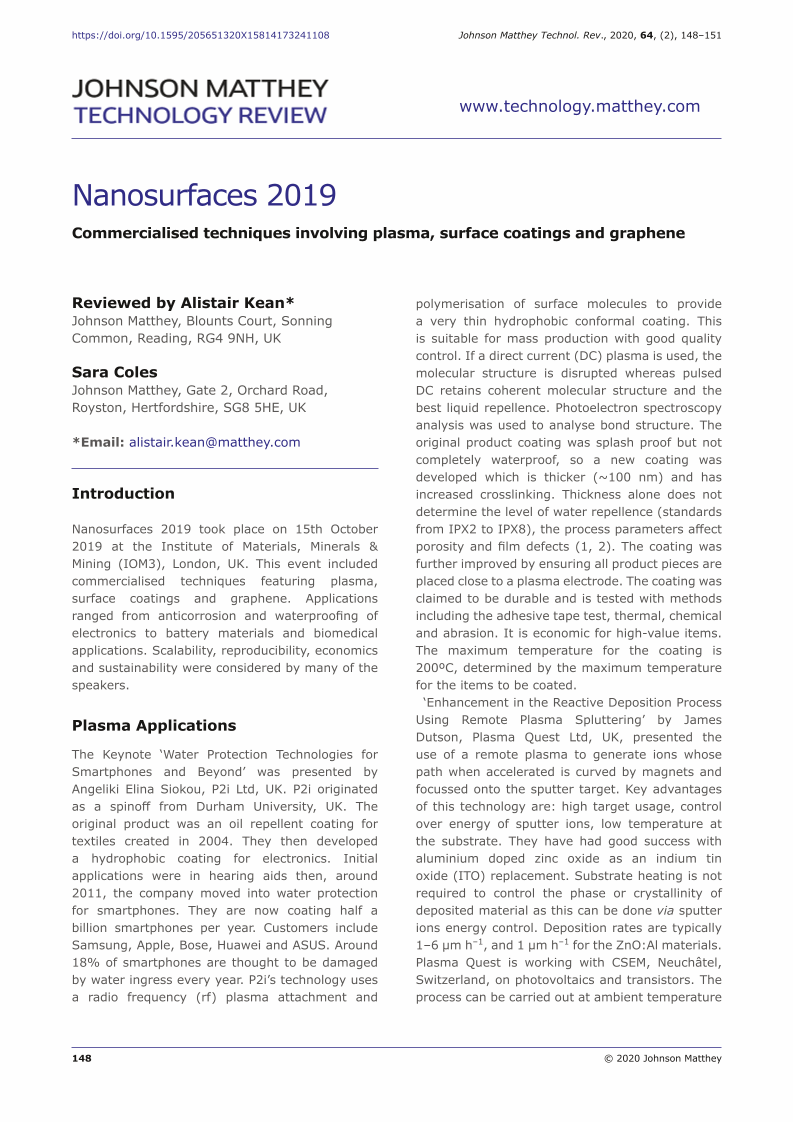



Nanosurfaces 2019, Page 1 of 1
< Previous page Next page > /docserver/preview/fulltext/jmtr/64/2/Nanosurfaces_16a_Imp-1.gif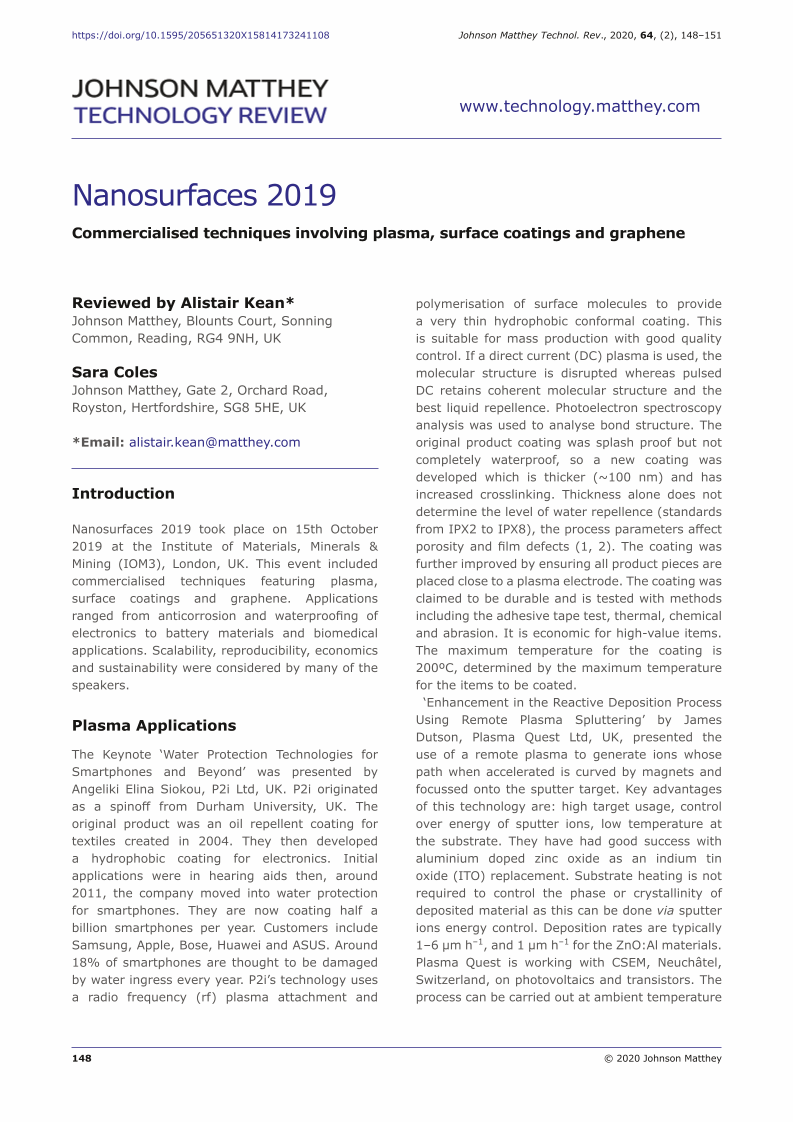
There is no abstract available.
© Johnson Matthey