-
oa Guest Editorial: Facility Process Safety and Control
- Source: Johnson Matthey Technology Review, Volume 67, Issue 1, Jan 2023, p. 2 - 3
-
- 30 Sep 2022
- 21 Dec 2022
Preview this article:
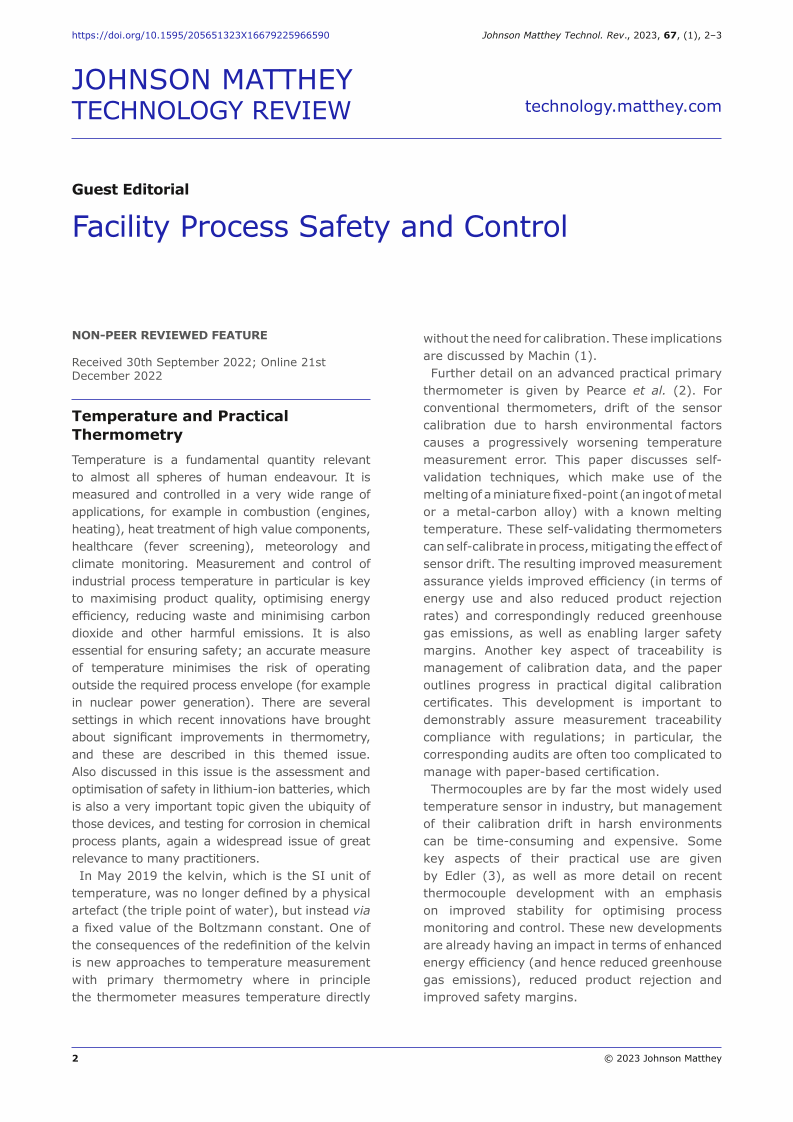



Guest Editorial: Facility Process Safety and Control, Page 1 of 1
< Previous page Next page > /docserver/preview/fulltext/jmtr/67/1/Editorial_16a_Imp-1.gif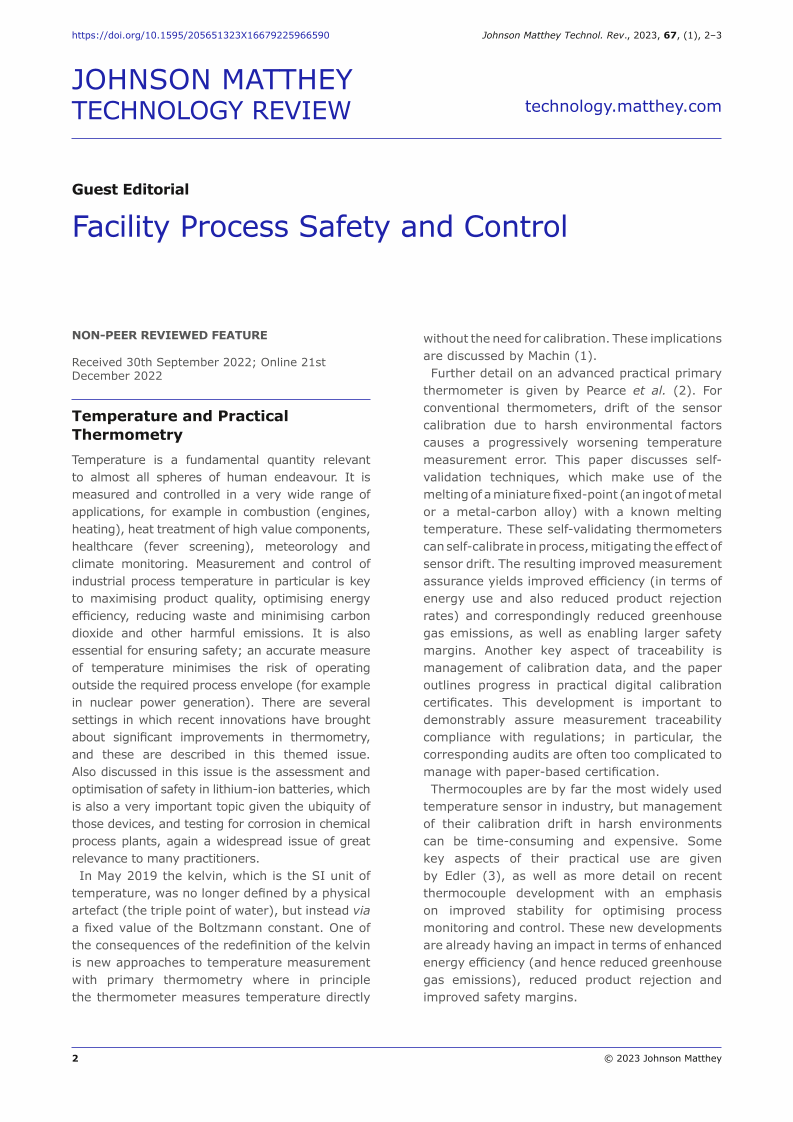
There is no abstract available.
© Johnson Matthey