-
oa Guest Editorial: Electrochemistry at Johnson Matthey
- Source: Johnson Matthey Technology Review, Volume 62, Issue 2, Apr 2018, p. 132 - 133
-
- 01 Jan 2018
Preview this article:
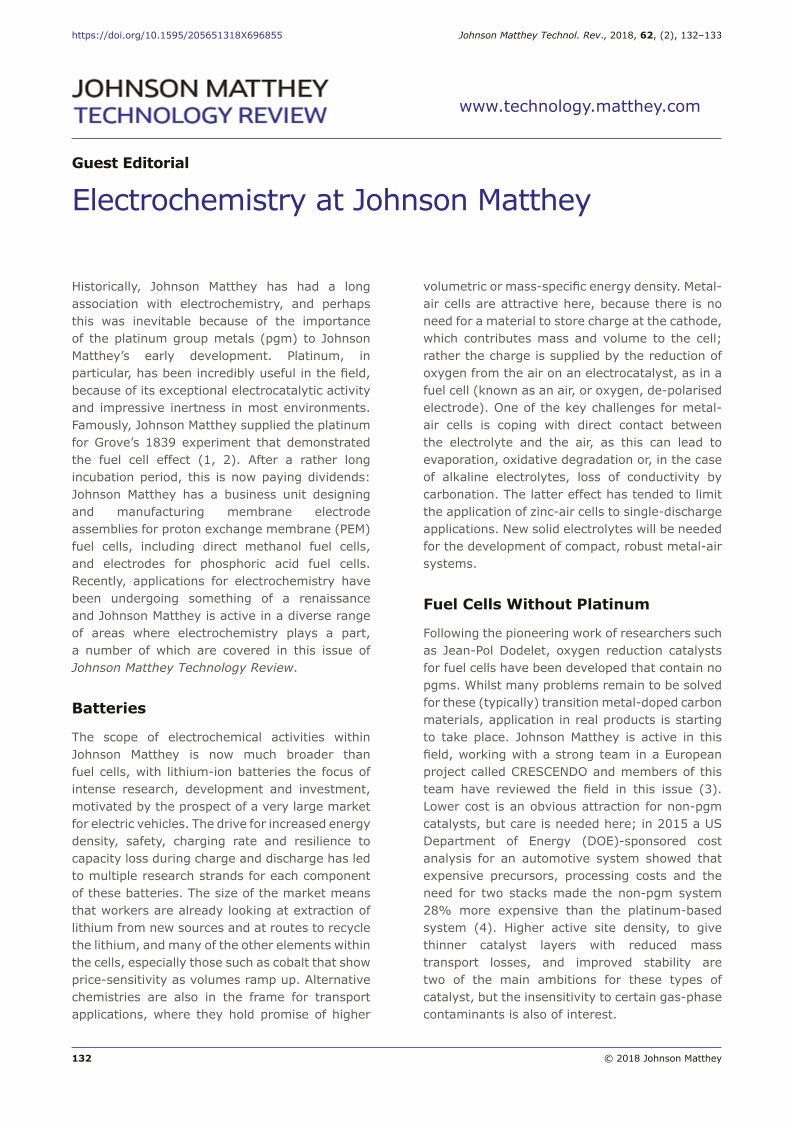



Guest Editorial: Electrochemistry at Johnson Matthey, Page 1 of 1
< Previous page Next page > /docserver/preview/fulltext/jmtr/62/2/Editorial_16a_Imp-1.gif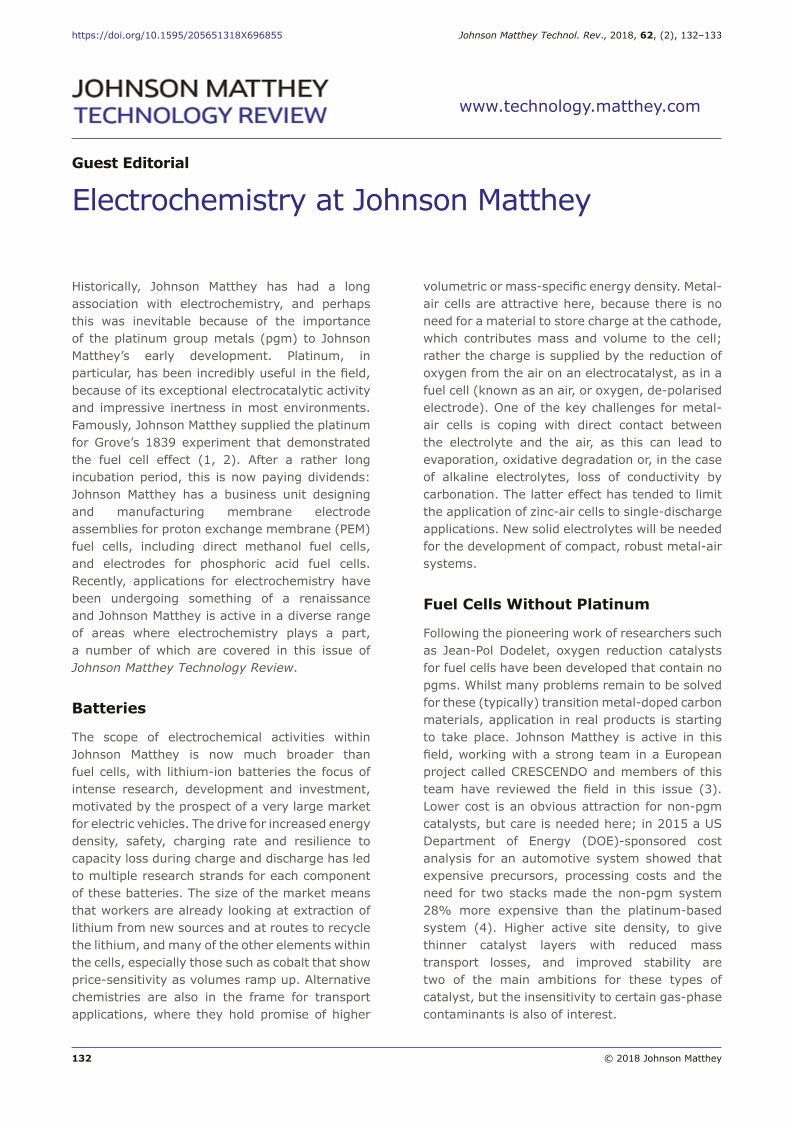
There is no abstract available.
© Johnson Matthey