-
oa 9th International Conference on Mechanochemistry and Mechanical Alloying (INCOME 2017)
Novel techniques to prepare materials for pharmaceutical, medical and other applications
- Source: Johnson Matthey Technology Review, Volume 62, Issue 4, Oct 2018, p. 426 - 428
-
- 01 Jan 2018
Preview this article:
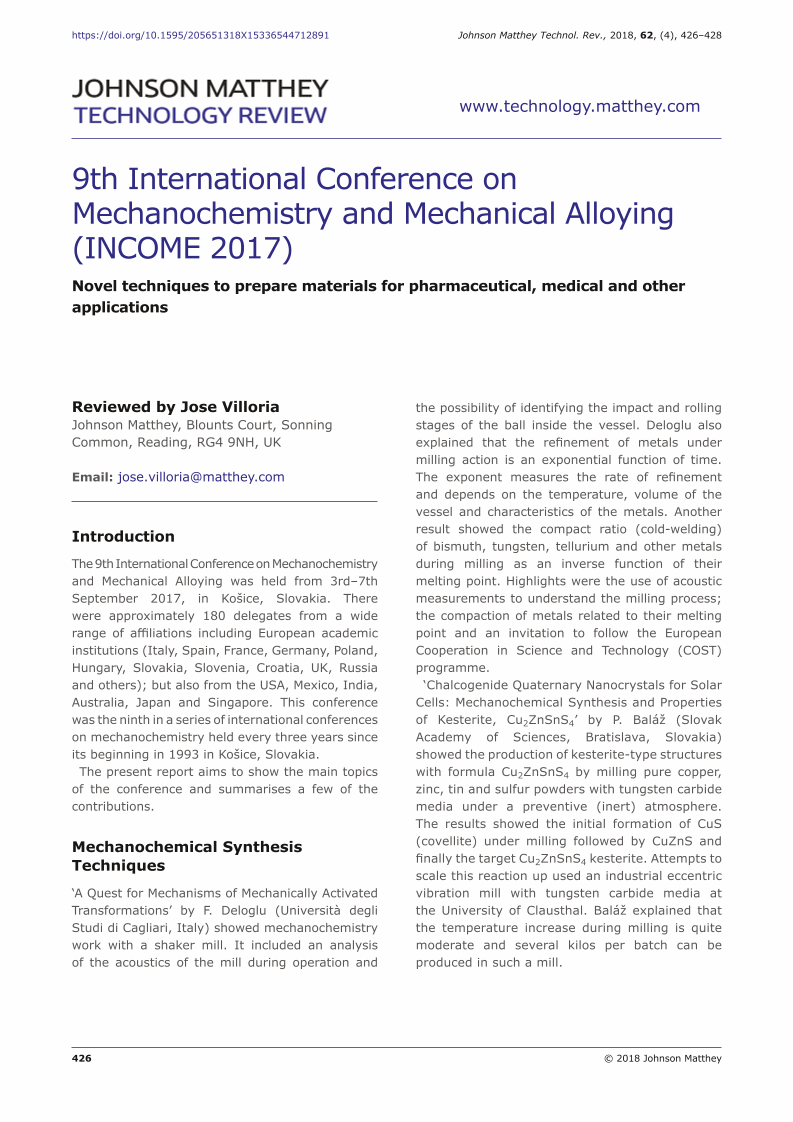



9th International Conference on Mechanochemistry and Mechanical Alloying (INCOME 2017), Page 1 of 1
< Previous page Next page > /docserver/preview/fulltext/jmtr/62/4/Villoria_16a_Imp-1.gif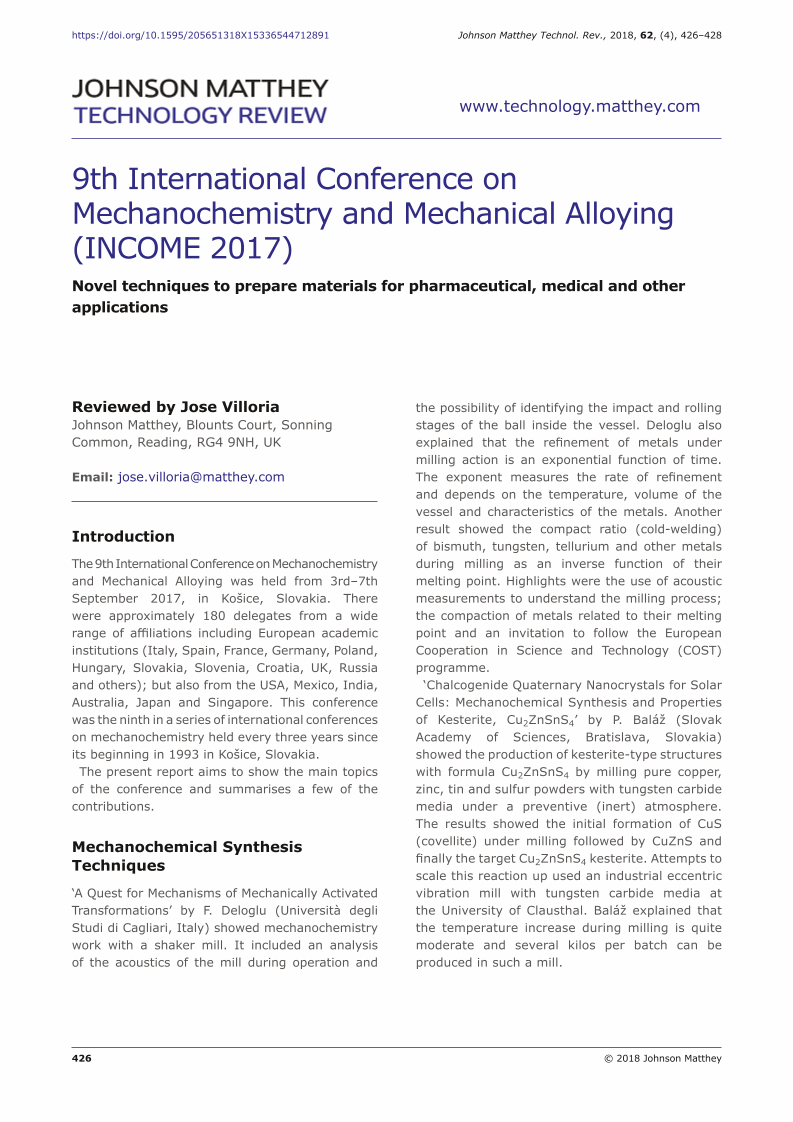
There is no abstract available.
© Johnson Matthey